- +1
【复材资讯】“自循环电化学”高效回收锂电池正极材料
研究背景
锂离子电池(LIBs)的广泛应用加剧了对锂资源的需求,而废旧电池回收技术仍面临高能耗、大量化学试剂消耗以及污染物排放等问题。目前常用的火法和湿法冶金工艺虽然可回收金属元素,但通常涉及能源、化学或废物密集型过程,存在资源利用率低、环境负担重、产品纯度受限等缺点。此外,传统湿法冶金方法回收的锂主要以Li2CO3或Li2SO4形式存在,而高镍正极材料制造需要LiOH,这势必导致了额外的原料转换步骤。因此,开发一种绿色、高效、循环利用的电化学回收策略对于可持续电池产业至关重要。

图1| 传统湿法冶金过程需要化学试剂的大量投入并产生废液排放。
【工作简介】
本研究提出了一种自循环电化学回收策略,利用三腔体多孔固体电解质(PSE)电解池,在高锂离子传输效率(tLi⁺> 90%)和高电流密度(>100 mA/cm2)条件下,实现了Li2SO4溶液的高效电解,生成高纯度LiOH和H2SO4。该方法避免了额外化学原料的使用,并可循环利用酸/碱,实现了全过程零废液排放。最终回收的高纯度LiOH(>99.7%)和Co(OH)2(>99.8%)可直接用于新电池制造。本研究为LIBs的可持续回收提供了一种绿色、高效的解决方案。
【核心内容】
传统湿法回收方法使用H2SO4等强酸浸出正极材料,再用NaOH或NH4OH沉淀分离金属离子,导致大量化学试剂的投入,并产生Na2SO4、NH4+等废液并伴随最终产物中的杂质。本研究采用电化学酸/碱再生策略,避免了外部阳离子引入,并提高了资源利用效率。此外,采用三室固体电解质电解池可实现Li+的定向迁移,相比传统两腔体MEA或多腔体,提高电解选择性和能效。
【实验原理】
作为最常见和最昂贵的正极材料之一,本研究选择LiCoO2(LCO)作为模型材料,并将这种方法扩展到其他过渡金属。自循环电化学回收主要包括三个步骤实现自循环利用:
1)电化学法酸/碱再生:利用三室固体电解质电解池,在低至0.36V的起始电压下,将Li2SO4溶液电解生成高纯度LiOH和H2SO4。
2)酸浸溶解正极材料:利用电解生成的H2SO4进行正极材料的化学计量酸浸,实现锂和过渡金属的高效溶解。
3)金属分离:过渡金属与锂离子的,利用电解生成的LiOH沉淀过渡金属,分离得到Co(OH)2、Ni(OH)2等高纯度金属氢氧化物。
4)循环利用:最终回收的Li2SO4溶液可重新进入电解过程,实现自循环回收,无需额外化学试剂投入。
【图文解析】
自循环电化学电池回收系统包括以下三个主要步骤:(1)在PSE反应器中电解硫酸锂盐,(2)溶解LiCoO2,(3)通过Co沉淀分离Li/Co。为了以高效地电化学方法从Li2SO4电解中生产酸化和碱化流,本工作采用了三腔体PSE反应器,并结合了析氢反应(HER)和氢氧化反应(HOR)。中间腔体PSE层由致密但具有渗透性的阳离子导电聚合物颗粒组成, 并被两种类型的阳离子交换膜夹在中间:一种用于质子交换(PEM),另一种用于锂离子传输(CEM)。在HER-HOR电解过程中,Li2SO4溶液通过PSE层室连续流动,在电场的驱动下,在阳产生的质子穿过PEM向中间层移动,并将Li+向阴极室移动形成LiOH。PSE层不仅有利于阴极和阳极之间阳离子的高效传导和目标产物的形成,还降低了欧姆阻抗,提高了各种电催化反应的离子传输效率和系统稳定性。
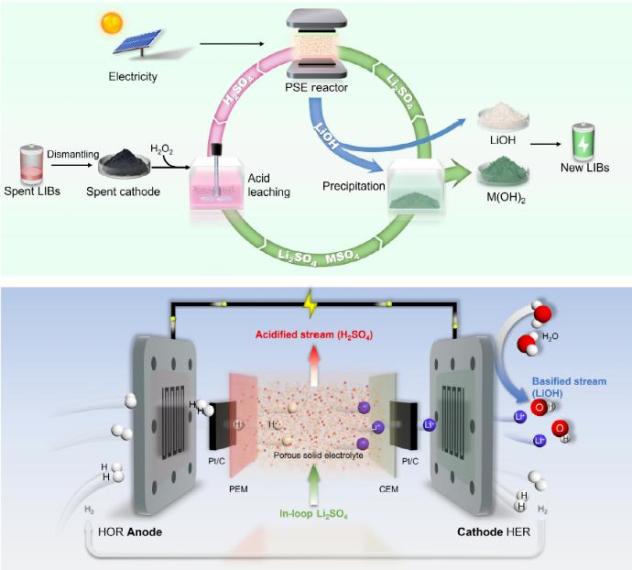
图2| 自循环电化学策略在锂离子电池正极回收中的应用:上图,自循环电化学电池回收工艺采用 PSE 反应器进行 Li2SO4 分解、酸浸及锂与过渡金属的分离(通过 LiOH 沉淀)。所有工序能量均来自于电能输入,最终产物为高纯度 LiOH 和 Co(OH)2(或者三元前驱体),全过程中不产生化学排放。下图,三腔电化学池配置的多孔固态电解质(PSE)电解槽设计示意图。
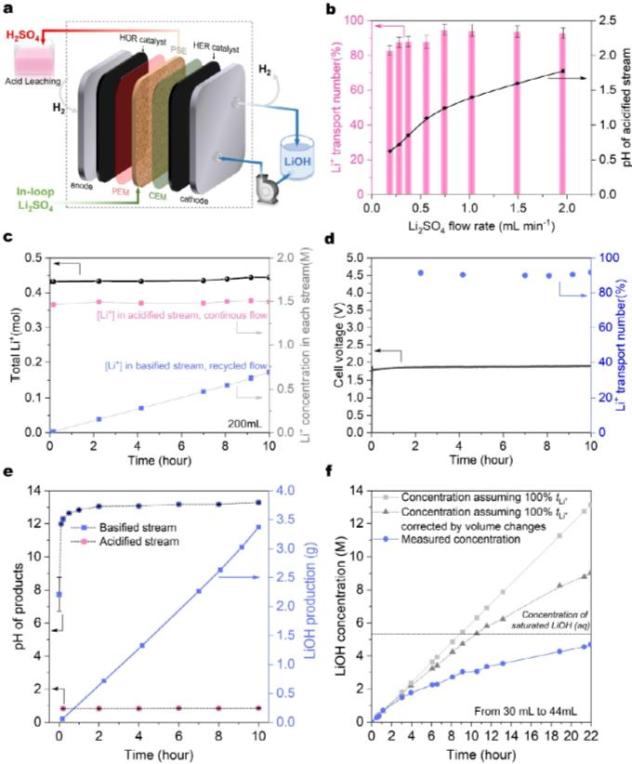
图3| 电化学电池回收反应工艺中的电化学酸/碱再生过程及性能:a, PSE 反应器电解生成硫酸和氢氧化锂的示意图,Li2SO4溶液流入中间腔体并产生硫酸,阴极产生高纯度氢氧化锂。b, 在 400 mA 电流下,PSE 反应器的 Li+ 迁移数(tLi⁺)及从中间腔体生成的酸的 pH 值在不同电解液输入流速下的变化。c, 在一个完整电解周期中,中间腔体产出液(红点)及阴极电解液(蓝点)的 Li+ 浓度随电解时间的变化,以及 Li+ 质量平衡分析。d,PSE 反应器的电压和效率(基于tLi⁺)。e, 中腔酸化流和阴极腔碱化流的 pH 值随时间变化,以及一个电解周期内 PSE 反应器生成的 LiOH 质量。f, PSE 反应器可获得接近饱和的高浓度 LiOH 溶液。
根据酸浸后最终溶液的pH值(~4.0~4.8),质子利用效率在99.9%以上,这意味着在钴沉淀步骤中,阴极产生的LiOH只需要不到0.1%来中和未使用的酸。同时,为了最大限度地通过Co(OH)2沉淀回收Co,在沉淀过程中需要适量的LiOH来提高pH。如图4a所示,存在一个代表Co2+沉淀过程的pH平台。为了达到该pH值以获得较高的Co回收效率,阴极产生的LiOH约有65%被消耗掉(图4a),这接近于在上述定量分析中讨论的理论值66.7%。因此,经过一个循环后,Li2SO4盐分裂过程中剩余的35% LiOH溶液和Co(OH)2沉淀是最终产物,该溶液再次回到Li2SO4中进行下一个循环。
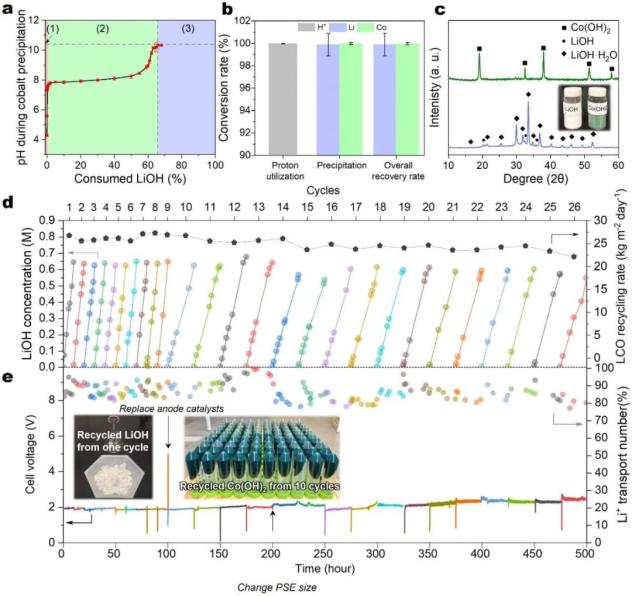
图4| LCO 阳极回收全过程:钴沉淀、产品相纯度及稳定性测试:a, 酸浸溶解正极材料和钴沉淀过程的 pH 变化图:区域(1)表示酸浸未反应酸的中和(2LiOH + H2SO4 = Li2SO4 + 2H2O,少于1%);区域(2)表示钴沉淀过程(2LiOH + CoSO4 = Li2SO4 + Co(OH)2);区域(3)表示剩余的 LiOH 作为最终回收产物。Li2SO4溶液在区域(1)和(2)中被再生。b, 单次循环的转化率,包括质子利用率、Li 和 Co 在沉淀过程中的转化及整体转化率。c, 回收的锂和钴产品的粉末 XRD 图谱和照片。d, PSE 反应器在电化学法酸/碱再生的稳定性测试(电解液使用每圈前一个循环后再生的Li2SO4电解液). e, PSE 反应器的电池电压和效率, 以及再生的高纯度LiOH和Co(OH)2。
电化学电池回收策略可以从LCO正极扩展到其他锂金属氧化物正极材料。我们选择了电动汽车中最常用的正极材料NMC (LiNi1/3Mn1/3Co1/3O2)以测试PSE反应器的适用性。
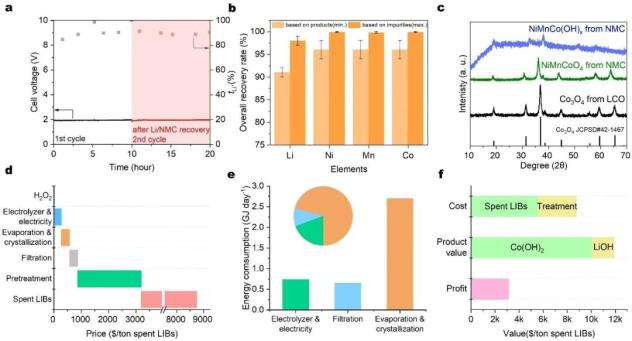
图5| 自循环电化学工艺在NMC 正极材料回收中的应用扩展及技术经济分析:a, PSE反应器在NMC正极材料回收过程中的电池电压及效率(高于90%)。b, NMC的金属回收效率。c, 回收的 NiCoMn(OH)x 及煅烧后的过渡金属氧化物(Co3O4 和 NiCoMnO4)的粉末 XRD 图谱。d-f, 自循环电化学工艺的成本分解的技术经济分析(TEA)和主要能耗分解。
最后,作者通过EverBatt 和Aspen模型分别评估了废电池处理以及结晶和过滤分离过程的成本,后两者的成本分别为每吨LIBs 294.9美元和298.6美元。再结晶、过滤和电解的碳足迹能耗分别为2.70、0.37和0.74 GJ/t,总能耗约为3.81 GJ/t。由此可见,在优化电解过程后,自循环电化学主要的能源消耗来自重结晶过程,该过程涉及大量的水蒸发,这表明在该过程中生产高浓度碱性溶液以减少系统中添加的水量的重要性。将废旧锂离子电池的成本与预处理费用合计计算后,处理废旧锂离子电池的总成本约为 8.9 千美元/吨。该成本有望通过回收产品的市场价值(基于当前市场价格)来抵消,例如,如仅考虑在该过程中回收的 0.14 吨 LiOH∙H2O和 0.31 吨 Co(OH)2,其市场总价值约为 12 千美元。因此,该工艺在经济可行性方面具有一定优势。
【结论】
本研究设计了一种高效的自循环电化学正极回收工艺,实现了从废旧电池正极中高效分离和回收Li及过渡金属。通过电化学方式将Li2SO4溶液分离为LiOH和H2SO4,实现酸碱再生以实现对废旧正极材料中锂和过渡金属的化学计量精确分离。该方法无需外部酸/碱化学品输入,不仅避免了废液处理过程,还减少了最终产品中潜在的阳离子污染。最终获得的LiOH(纯度>99.7%)和Co(OH)2(纯度>99.8%)的材料回收率分别超过91%和97%,能够直接用于新电池制造。此方向未来的研究将专注于提高固体电解质层Li+电导率,从而进一步提升电解过程的能量效率。此外,装置的规模化、对过渡金属的进一步分离和提纯,将有利于该方法在可持续电池产业和金属回收领域的应用。
来源:能源学人
免责声明:中国复合材料学会微信公众号发布的文章,仅用于复合材料专业知识和市场资讯的交流与分享,不用于任何商业目的。任何个人或组织若对文章版权或其内容的真实性、准确性存有疑议,请第一时间联系我们。我们将及时进行处理。
继续滑动看下一个轻触阅读原文
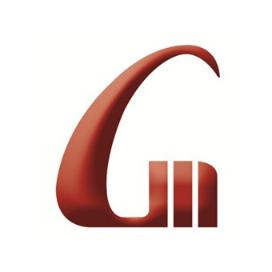
中国复合材料学会向上滑动看下一个
原标题:《【复材资讯】“自循环电化学”高效回收锂电池正极材料》
本文为澎湃号作者或机构在澎湃新闻上传并发布,仅代表该作者或机构观点,不代表澎湃新闻的观点或立场,澎湃新闻仅提供信息发布平台。申请澎湃号请用电脑访问http://renzheng.thepaper.cn。





- 报料热线: 021-962866
- 报料邮箱: news@thepaper.cn
互联网新闻信息服务许可证:31120170006
增值电信业务经营许可证:沪B2-2017116
© 2014-2025 上海东方报业有限公司