- +1
【复材资讯】碳纤维加热元件的制备及其对热塑性复合材料电阻焊接接头性能的影响
摘要
本文采用聚醚醚酮(PEEK)粉末悬浮浸渍工艺和PEEK树脂膜熔融浸渍工艺制备了两种不同的薄层碳纤维展宽布加热元件,并对碳纤维增强聚醚醚酮复合材料层合板的电阻焊接技术进行了实验研究。结果表明:采用“埋入式”电极布置方式,有效避免了电阻焊接过程中因加热元件裸露而产生的“边缘效应”现象。加热时间对焊接接头强度有明显的影响,接头强度随加热时间先增加后减小,在120 s时达到最大值28.1 MPa,断口失效模式从最初的粘接失效变为植入体与纤维的混合失式模式。对比粉末悬浮浸渍与熔融浸渍两种工艺制备的加热元件相应的焊接接头强度,在相同焊接工艺条件下前者相比后者提升15%。
作者
姚鑫1, 霍红宇1, 安学锋2, 张宝艳*1
( 1. 中国航空制造技术研究院,北京 101300;
2. 中航复合材料有限责任公司,北京 101300 )
正文
热塑性复合材料(Thermoplastic composites,TPC)具有可重复加工、焊接、耐溶剂、损伤容限高等特点,近年来国内外研究广泛,已在航空航天、交通、医疗等领域[1-4]应用。TPC在多种机型上均有应用,从角片、支架、油箱口盖等小制件逐渐向蒙皮、尾翼、壁板等大型制件发展[5-7]。基于热塑性树脂可熔融再加工的特点,衍生出TPC的焊接技术,与传统的连接方法相比,如机械连接和胶接,焊接技术能够提高生产效率,降低生产成本。其次焊接能够减少紧固件的数量、装配工作量,实现整体化的低成本制造。TPC的焊接技术主要包括电阻焊接[8]、感应焊接[9]、超声焊接[10]、激光焊接[11],上述各种焊接方式各有优劣。感应焊接虽然具有焊接速度快、可焊接体积大的优点,但其设备昂贵、焊接界面温度不均匀[12];超声焊接具有高效、清洁、低成本、操作简单、易于实现自动化等特点,但其对被焊接件厚度有一定要求,且工作过程中会产生较大的噪音[13];激光焊接具有焊接时间短、焊接强度高、振动应力小、适合焊接复杂结构件等优势,但其要求被焊接材料一方是对激光透明的,选材存在局限性[14]。
电阻焊接的基本原理是在两个待焊接面中间放置加热元件,加热元件在电流通过下产生焦耳热对界面进行加热使树脂熔融,并在压力作用下冷却固结形成焊接接头。相比于上述焊接方式,电阻焊接具有工艺流程短、设备简单灵活、费用低廉等优势[8]。电阻焊接技术在航空航天领域应用广泛,如A380机翼前缘、Fokker 50支线运输机主起落架舱门、A400M军用运输机的驾驶员座舱板主操纵面、Clean Sky项目中的多功能机体演示器(MFFD)的法兰盘等[15-16]。
加热元件作为电阻焊接中连接待焊接母材的“桥梁”,其作用至关重要,主要包括不锈钢金属网和碳纤维两类。国内外学者对不锈钢金属网加热元件进行了系统的研究,包括金属网的开口尺寸、粗细[17-18]及表面处理方式[19-20](喷砂、芳基重氮接枝和硅烷接枝)对焊接质量影响。Rohart等[21]研究了温度和湿度对碳纤维/聚苯硫醚(CF/PPS)复合材料焊接接头性能的影响,实验发现温度对焊接接头单搭接剪切强度(LSS)有明显影响,与室温相比在82℃时降低26%,在150℃时降低61%,另外PPS吸湿率极低,湿度对LSS影响较小。由于碳纤维加热元件在制备过程中存在与树脂之间的浸润性问题,碳纤维作为加热元件的研究相对较少。Ageorges等[22-23]研究了碳纤维单向带、织物作为加热元件对焊接接头性能的影响,发现碳纤维织物相比碳纤维单向带加热元件发热更均匀、加工窗口更宽并且焊接接头性能更优异(LSS提升69%);路鹏程等[24]采用CF/PPS混编织物作为加热元件,采用田口和方差分析方法,确定了该方式下电阻焊接的最优工艺参数(电流为12 A,压力为1.5 MPa,时间为30 min),接头单搭接剪切强度为17.9 MPa。
传统的碳纤维织物由于浸润效果差,造成焊接接头力学强度较差;不锈钢金属网虽然浸润效果优异,但存在与母材不匹配、增重、电偶腐蚀等问题;本文针对航空结构用碳纤维/聚醚醚酮(CF/PEEK)热塑性复合材料,采用粉末悬浮浸渍工艺改善纤维与树脂界面,制备了浸渍良好的薄层碳纤维展宽布加热元件。同时研究了加热时间对焊接接头力学性能的影响,并与熔融浸渍工艺制备的加热元件进行对比分析,为电阻焊接工程化应用提供研究基础。
1. 实验材料及方法
1.1 原材料
CF/PEEK复合材料层合板采用中国航空制造技术研究院复材中心自研的T800碳纤维/聚醚醚酮热塑性预浸料在高温压机上制备。玻璃布采用南京玻璃纤维研究设计院有限公司生产的EW100A,厚度为0.1 mm。薄层碳纤维展宽布采用TORAY T700 12K纤维编织,面密度为179 g/m2,厚度为0.14 mm。PEEK树脂膜由佛山市达孚新材料有限公司提供,单层膜厚度为0.08 mm。PEEK粉体选用浙江鹏孚隆公司生产的PFLUON® 8800UFP,粉体密度为1.30 g/cm3。双(2-乙己基)磺基丁二酸钠(AOT)作为高效分散剂用于PEEK悬浮液制备,上海阿拉丁生化科技股份有限公司生产。
1. 实验材料及方法
1.2 实验方法
(1)待焊接母材制备
预浸料铺层为[0/90]3s,按照铺层顺序依次铺贴后放入模具内,采用高温压机(青岛华博机械,HBSCR-100T)工艺参数为:接触压力0.3 MPa,10℃/min升至395℃后保温35 min,作用在预浸料叠层面积上的成型压力为3 MPa,带压自然冷却至室温后脱模。层合板纤维体积分数为(56±2)vol%,无损检验合格后机加工为待焊接母材(长101.6 mm,宽180 mm),为了获得粗糙的表面采用细砂纸对焊接区域进行打磨,并用丙酮溶液清洗,放入烘箱内烘干。
(2)加热元件制备
首先配制热塑性树脂PEEK悬浮液,室温条件下,在反应釜内加入10 kg的去离子水,并加入0.6 kg AOT,待其充分溶解后加入1 kg PEEK超细粉,搅拌5 h后,获得稳定PEEK悬浮液。然后,将碳纤维展宽布四周用金属框固定后放入盛有PEEK悬浮液的容器内浸渍,静置10 min后取出,放入高温烘箱内200℃烘干水分及其他助剂。分别将浸渍树脂与未浸渍树脂的碳纤维展宽布和PEEK树脂膜通过高温模压的方式复合制备加热元件。碳纤维展宽布两头用高温胶带固定防止树脂浸渍影响导电性能,上下两层树脂膜在碳纤维织物表面形成富树脂层。热压工艺参数为:10℃/min升温至390℃、成型压力2 MPa,保温30 min,最后将制备的加热元件裁剪为标准尺寸,具体流程如图1所示。采用粉末悬浮浸渍工艺制备的薄层碳纤维展宽布加热元件,记为HE-1。作为对比实验,采用熔融浸渍工艺制备了同样的薄层碳纤维织物加热元件,记为HE-2。两种加热元件的树脂含量均为(50±3)wt%。
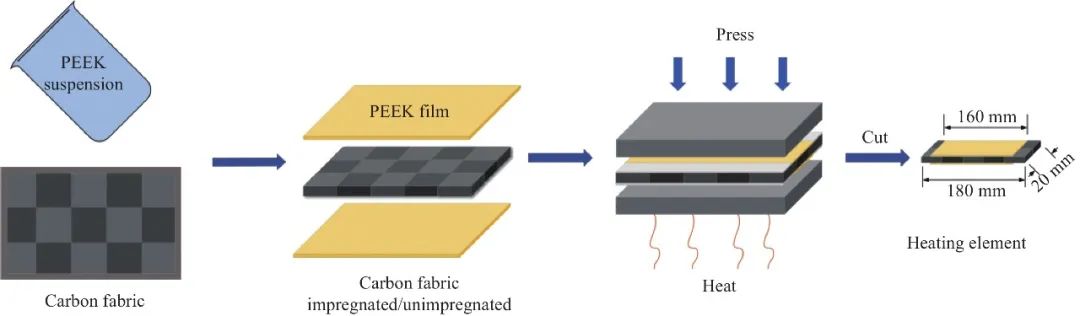
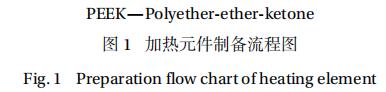
(3)绝缘层制备
采用热压的方式制备EW100 A/PEEK绝缘层,在单层玻璃布EW100 A上下各铺放一层PEEK树脂膜后放入模具内,热压工艺参数为10℃/min升温至390℃,成型压力2 MPa,保温30 min。
(4)电阻焊接设备的组装及焊接工艺
电阻焊接装置:由电源、监控系统、压力系统组成,如图2(a)所示。电源采用80 V、22 A大功率直流电源(南京艾德克斯电子有限公司,IT-M3122);监控系统包括焊接过程中压台高度变化记录及多通道热电偶记录仪(优利德科技股份有限公司,UT3208)监测焊接接头内部温度;压力系统采用伺服电机驱动螺杆使压头下移提供焊接所需压力。在焊接过程中,放置绝缘压力块在待焊接母材上下进行压实。
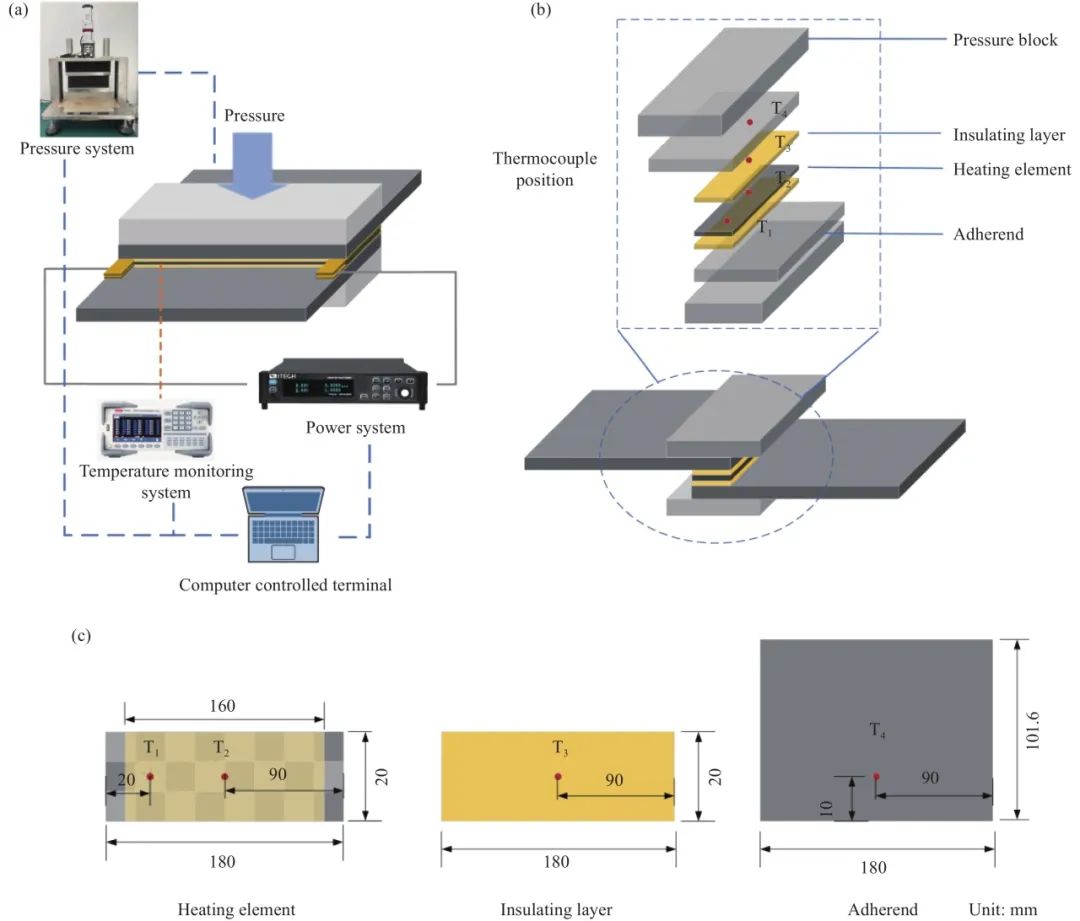

温度监测:焊接过程中采用4个K型热电偶(开普森兴化市苏玛电器仪表有限公司)对焊接接头内部温度及待焊接母材表面温度进行监测,热电偶用耐高温绝缘胶带包裹避免受到电流干扰影响测量结果。K型热电偶分别放置于图2(b)、图2(c)中T1~T4位置处:T1、T2放置于加热元件表面中心线上,T1距离电极20 mm处,T2位于加热元件中心处距离右侧电极90 mm,T3位于绝缘层中心处,T4位于带焊接母材表面与T2、T3在同一截面上,具体如图2(c)所示。由于热电偶在焊接接头中引入缺陷,降低搭接剪切强度,因此在搭接剪切试验中没有使用热电偶。
电阻焊接工艺:在电阻焊接过程中,需要经历4个热阶段,分别是加热、熔融、结晶、冷却。为了进行有效的电阻焊接实验,需要确定焊接工艺参数,包括压力水平、电压水平、加热时间。通过前期实验分析,采用27 V作为加热电压,0.75 MPa作为压力值,焊接时间分别为75、90、105、120、135 s。
1. 实验材料及方法
1.3 表征与测试
(1)金相显微镜检测
采用显微镜(ZEISS Smartzoom 5)对制备的加热元件及焊接接头截面进行金相分析。
(2)热失重分析
采用热失重分析仪(TGA5500,TA Instruments)评价制备的两种加热元件的耐热性能,气氛为氮气(吹扫速率:40 mL/min),室温升至800℃,升温速率为10℃/min。
(3)扫描电子显微镜检测
采用场发射扫描电子显微镜(Quanta 450 FEG)观察力学测试后试样的破坏断面,试样喷铂后再进行观察,加速电压选择15 kV。
(4)单搭接剪切强度测试
参照ASTM D5868—01标准[25],试样焊接完成后对其进行机械加工,得到搭接剪切试样,单侧长度为101.6 mm,宽度25 mm,搭接宽度为20 mm。使用Instron 5982万能试验机对焊接试样进行单搭接剪切强度测试,拉伸速率设置为13 mm/min,计算公式如下所示:
式中:τ为单搭接剪切强度(MPa);L为搭接长度(mm);b为搭接宽度(mm);Fmax为最大拉伸力(N)。每次取5根试样用作测试,取平均值。
2. 结果与讨论
2.1 加热元件性能分析
加热元件作为载体其性能好坏至关重要。由于PEEK树脂流动性较差,采用熔融浸渍工艺很难将碳纤维织物浸渍充分,本文采用粉末悬浮浸渍工艺改善了树脂对纤维浸渍效果差的现象。两者截面金相照片如图3所示,对比发现采用熔融浸渍工艺获得的效果明显不如粉末悬浮浸渍工艺,碳纤维展宽布中间大部分区域存在孔隙,仅在展宽布表面形成树脂层。由于两种加热元件采用的都是相同的PEEK树脂,故热稳定性差异不大,二者初始分解温度(N2气氛)分别为553℃(HE-1)、552℃(HE-2),TGA曲线如图4所示。在焊接过程中应当合理控制电压水平及加热时间,避免焊接界面处的温度高于PEEK树脂的初始分解温度,造成基体及母材损伤。
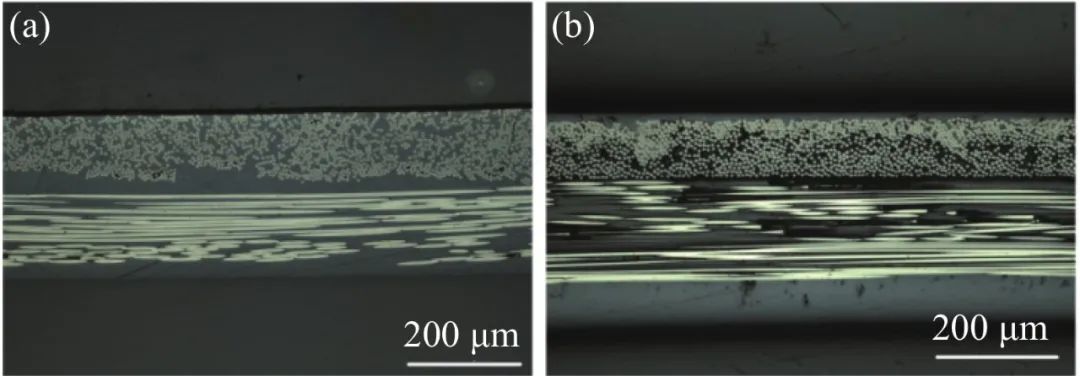
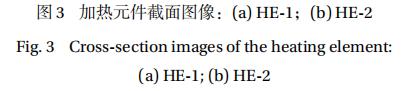
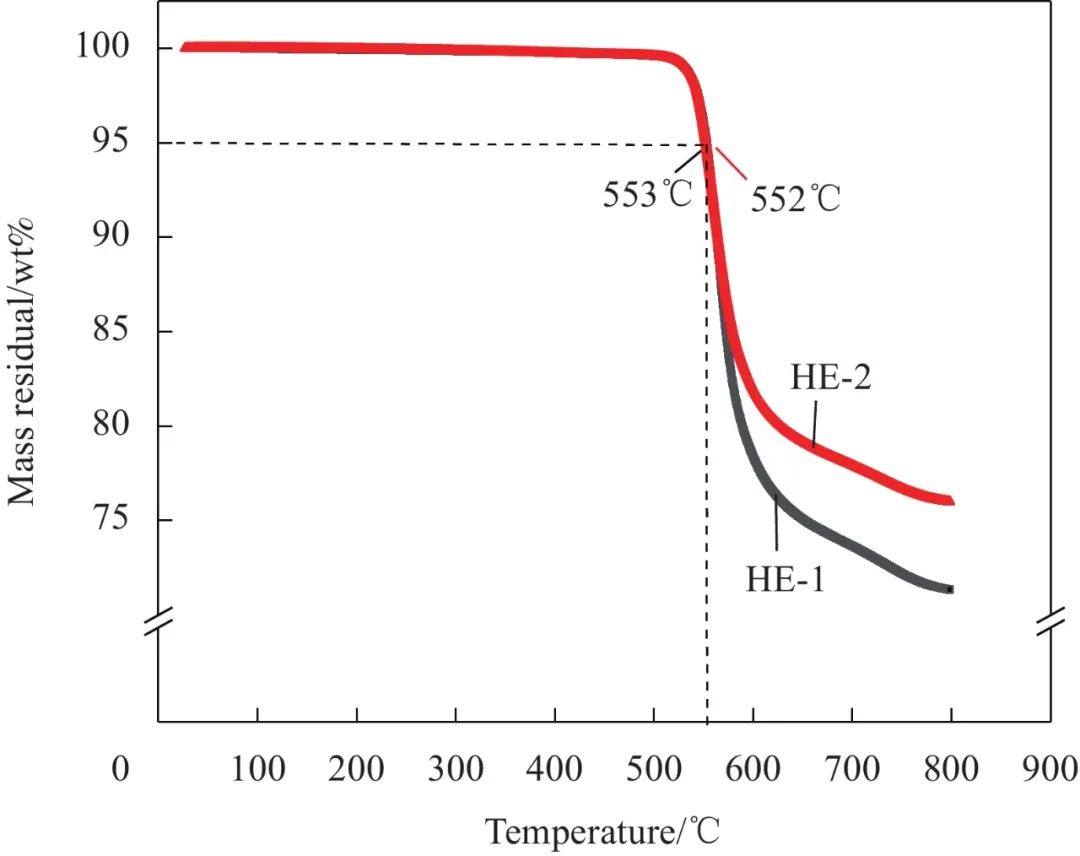
在进行电阻焊接操作时,需要准确地知道加热元件的电阻,以便确定电压强度,因此电阻值是一个重要的因素。使用数字万用表(优利德科技股份有限公司,UT804)检测了两种加热元件单位长度的电阻值(宽度为20 mm),具体如表1所示。
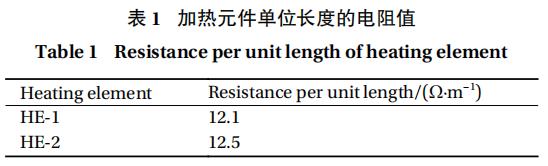
为了研究加热元件的电压循环响应特性,将加热元件(长180 mm,宽20 mm)两侧与黄铜电极连接并施加一定压力,表面随机放置5个K型热电偶检测温度,在空气条件下施加不同电压达到稳态后进行温度测量。温度测量结果的平均值与施加电压强度的关系如图5所示,可以看出两种加热元件表面温度与电压基本呈线性关系。另外,在稳态条件下采用热成像仪(优利德科技股份有限公司,UTi260B)分析了加热元件表面的温度分布情况,如图6所示。不同电压下加热元件的表面温度与图5中记录的数据相近。两种加热元件表面的温度分布情况也类似,表明加热元件浸渍效果对其自身的发热状态影响较小。
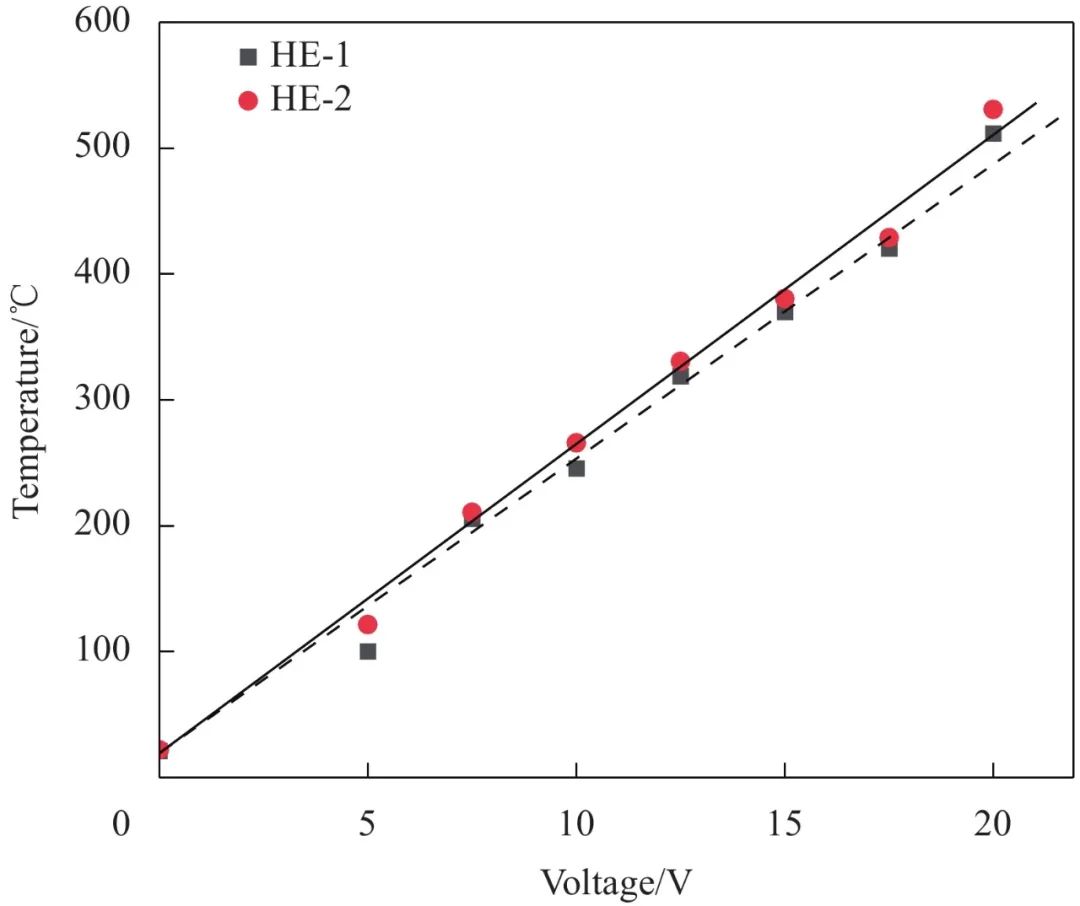
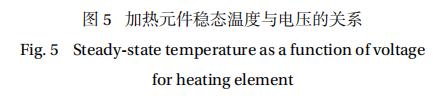
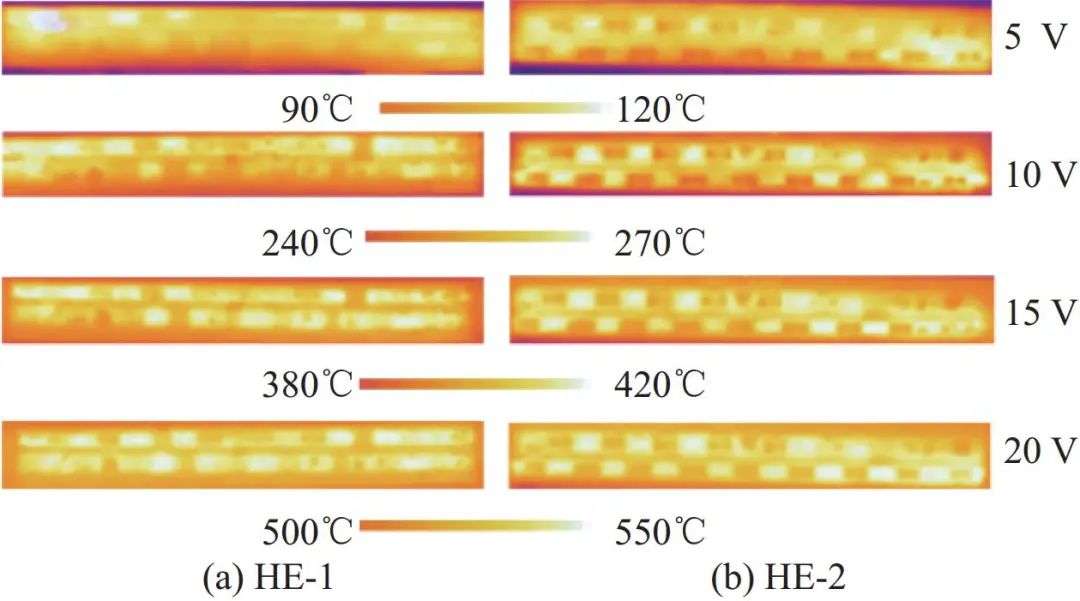
2. 结果与讨论
2.2 焊接组件内部的温度分布
焊接层内均匀的传热、温度分布是获得焊接接头最佳性能的关键。为了探究焊接内部的温度情况,采用多通道热电偶仪记录了焊接过程中焊缝内部及待焊接母材表面的温度分布情况。两种加热元件在相同电压下均观察到了相似的温度分布情况。HE-1作为加热元件在焊接工艺参数为电压27 V、压力0.75 MPa、加热时间135 s下焊接试样的温度-时间曲线,如图7所示。从温度-时间曲线可以观察到加热元件在长度方向上产生了温度梯度,电极附近温度(T1)略低于中心处温度(T2),主要是由于“埋入”电极的方式避免了边缘效应。传统的电极布置方式(图8(a))导致电极附近加热元件暴露在空气当中,因微弱的热对流造成散热不均匀导致边缘温度过高的现象,即边缘效应[8];然而,采用“埋入”电极的方式(图8(b))避免了加热元件暴露在空气中,降低了热对流对散热的影响,由于铜片的热导率较高,电极边缘处的热量通过铜片散失,导致两侧温度略低于中心温度。另外观察热电偶T2、T3、T4可以发现,焊接接头内部厚度方向上由于热传导而产生温度梯度,比较热电偶T2与T3可以发现,绝缘层的加入降低了待焊接母材表面的温度。
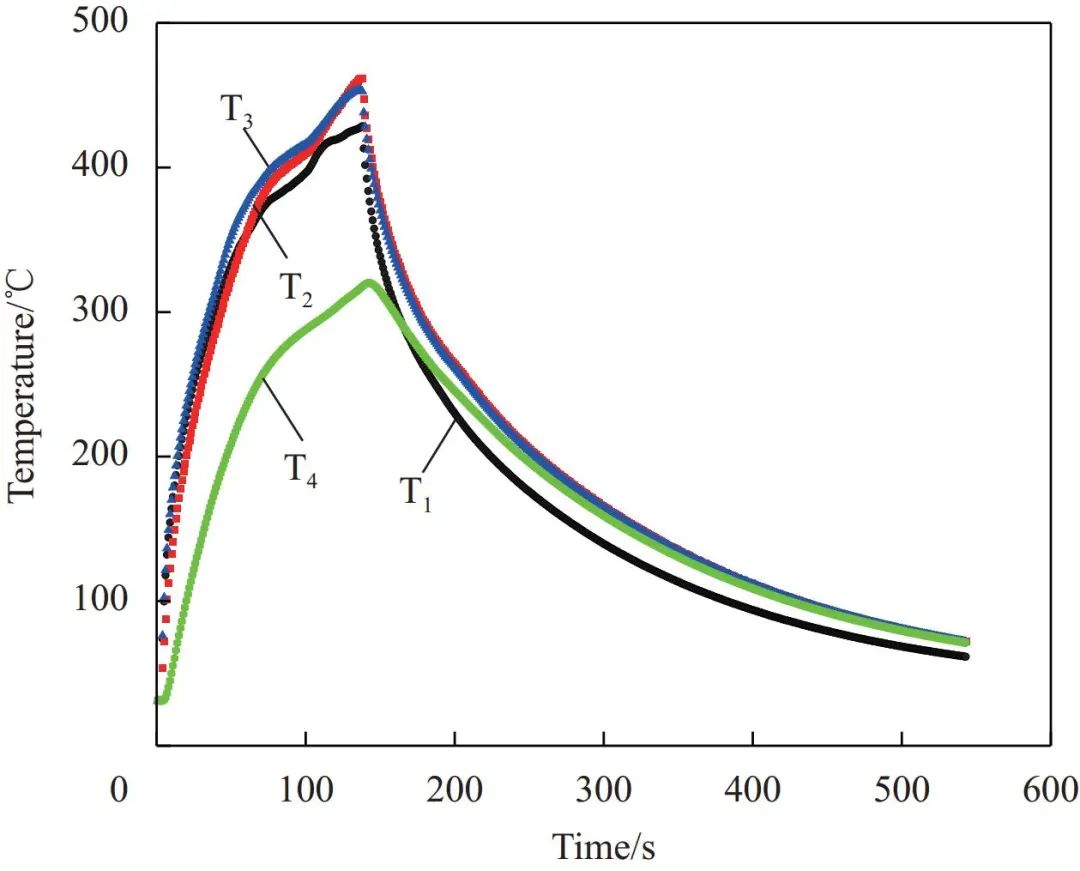

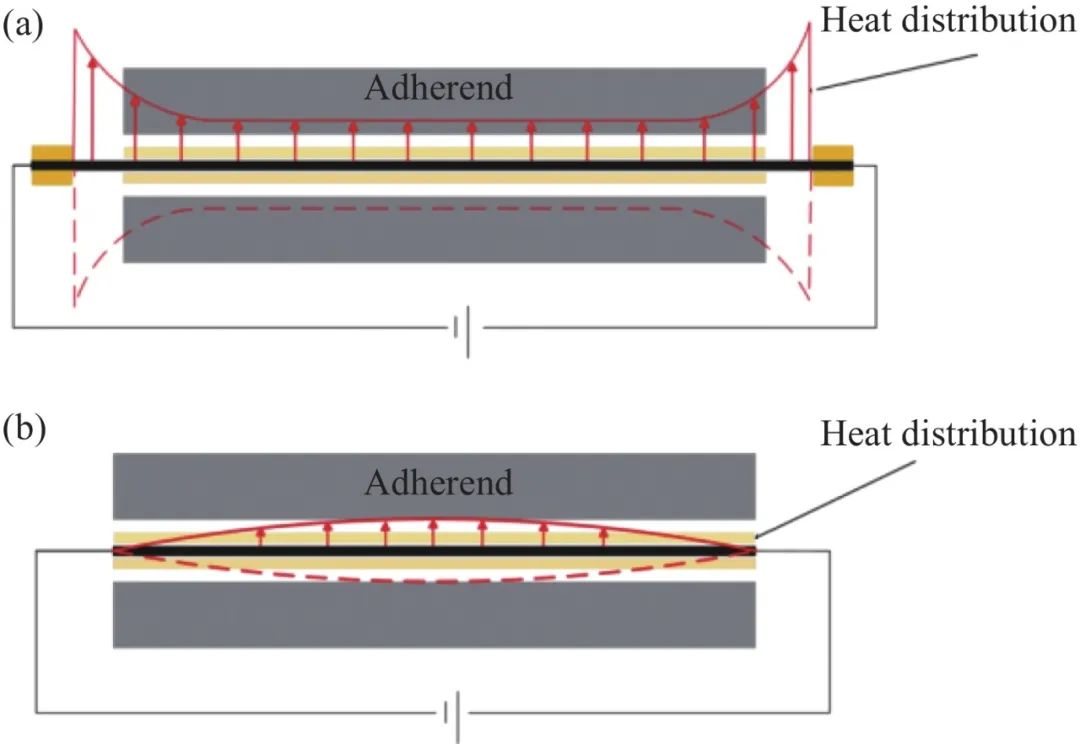
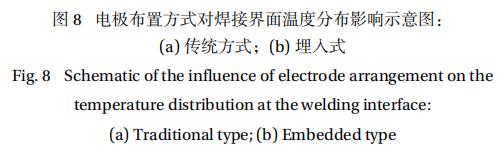
在焊接过程中不添加绝缘层极易出现局部漏电的现象[8,22-23],即加热元件表面树脂被挤出后导电纤维与待焊接母材表面的纤维接触构成导电回路,造成待焊接母材受损严重,无法进行焊接实验。而添加绝缘层后不仅可以避免焊接过程中的漏电现象,还可以获得更宽的焊接工艺窗口。
2. 结果与讨论
2.3 加热时间对焊接接头性能的影响
为了研究加热时间对焊接接头性能的影响,分别采用两种加热元件(HE-1、HE-2)进行焊接试验。图9为两种加热元件在电压27 V、压强0.75 MPa的焊接工艺条件下焊接接头LSS与加热时间的关系。结果表明:焊接接头LSS随加热时间先增加后减小,在75 s时达到最小值11.9 MPa(HE-1)、12.1 MPa (HE-2);在120 s时达到最大值28.1 MPa (HE-1)、23.7 MPa (HE-2),相比提升136.1% (HE-1)、95.7% (HE-2);当时间达到135 s时,焊接界面处由于温度过高造成界面损伤导致焊接接头强度下降。
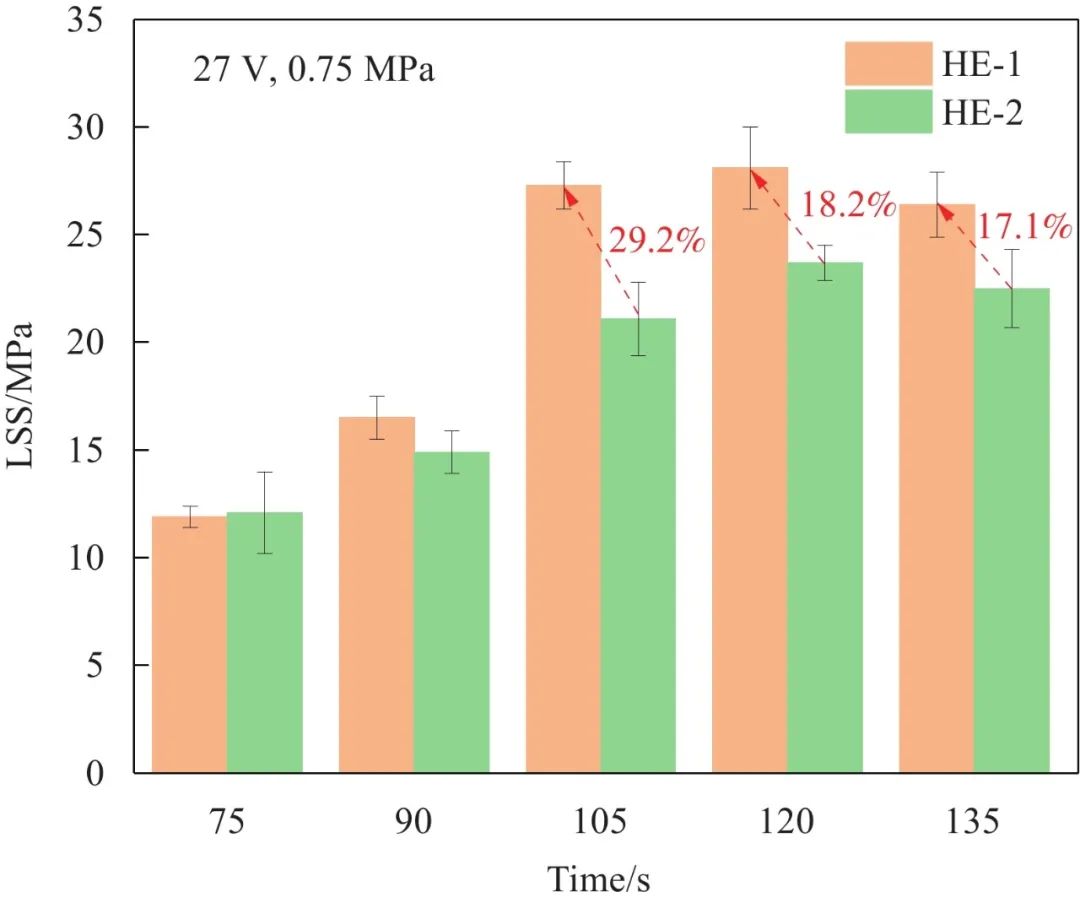

对比两种加热元件的焊接接头单搭接剪切强度可以发现,当加热时间为75 s时,两种加热元件焊接接头LSS相近,但随着加热时间的增加,HE-1焊接接头LSS均高于HE-2。由于加热元件HE-2中树脂对纤维的浸渍效果较差存在大量缺陷,但随着焊接时间的增加,树脂在碳纤维展宽布内部有充分的时间流动,填补了少量缺陷,树脂/纤维界面强度提升,两者接头强度差距逐步缩小,由加热时间为105 s时的29.2%变为135 s时的17.1%。对比两种加热元件焊接接头截面金相照片(图10)发现,采用HE-2加热元件在焊接结束后,接头内部仍然存在部分孔隙,相比之下HE-1接头内部孔隙则较少,也说明了HE-1焊接接头强度较高的原因。
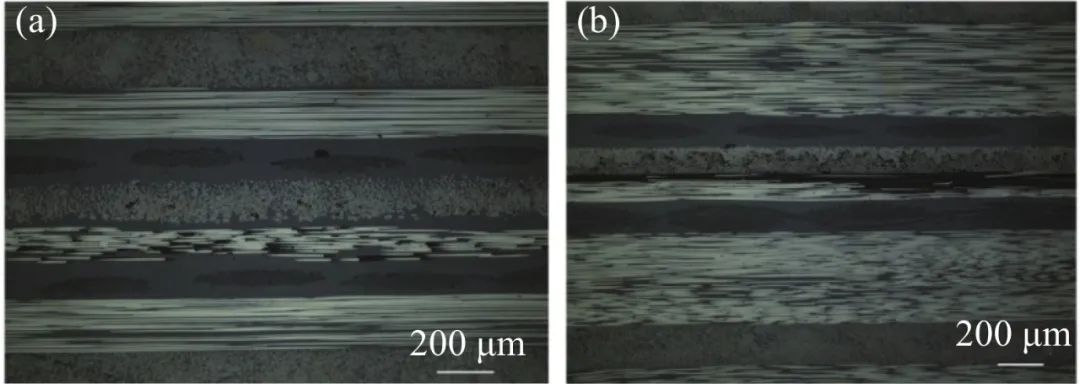

2. 结果与讨论
2.4 焊接接头断口分析
焊接接头的失效模式随着加热时间的不同表现为不同的形式,对于加热元件HE-1,当加热时间为75 s时接头为粘接失效模式(图11(a)),即聚合物基体与待焊接母材界面两侧树脂未能充分熔融并扩散缠结,界面强度低,焊接接头强度仅为11.9 MPa;当加热时间为90 s时接头失效模式转变为植入体失效(图11(b)),即加热元内部撕裂,接头强度提升至16.5 MPa;加热时为105 s时焊接界面充分固结,接头强度进一步提升表现为植入体+纤维失效的混合模式,如图11(c)中虚线部分,可以观察到加热元件的撕裂及焊接母材表面纤维的撕脱,表明焊接质量得到明显提升,此时接头强度为27.3 MPa;当加热时间达到120 s时待焊接母材表面纤维撕脱现象更显著(图11(d)虚线部分),接头强度达到最大值28.1 MPa。相比之下,对于加热元件HE-2,在加热时间为75 s时焊接接头表现为粘接+植入体失效模式(图11(e)),加热元件内部存在大量裸露的干纤维,焊接接头LSS仅为12.1 MPa;当加热时间延长至90、105 s时,焊接接头失效模式为植入体失效(图11(f)、图11(g)),接头强度提升;当加热时间达到120 s时焊接接头为植入体+纤维混合失效模式,母材表面存在部分纤维撕脱的现象(图11(h)),焊接接头LSS提升至23.7 MPa。随着加热时间的进一步增加(135 s时),HE-1、HE-2焊接接头内部温度过高导致界面损伤产生缺陷,接头强度均有所下降。结果表明:采用粉末悬浮浸渍工艺制备的加热元件HE-1相比熔融浸渍工艺制备的加热元件HE-2焊接接头强度有明显的提升且接头强度最高时焊接接头纤维撕脱的现象更显著。焊接接头强度提升原因如图12所示,粉末悬浮浸渍工艺将PEEK粉体分散于碳纤维丝束之间,原位熔融浸渍。相比于传统热熔法缩短了树脂热熔流动的距离,提升了浸润性。
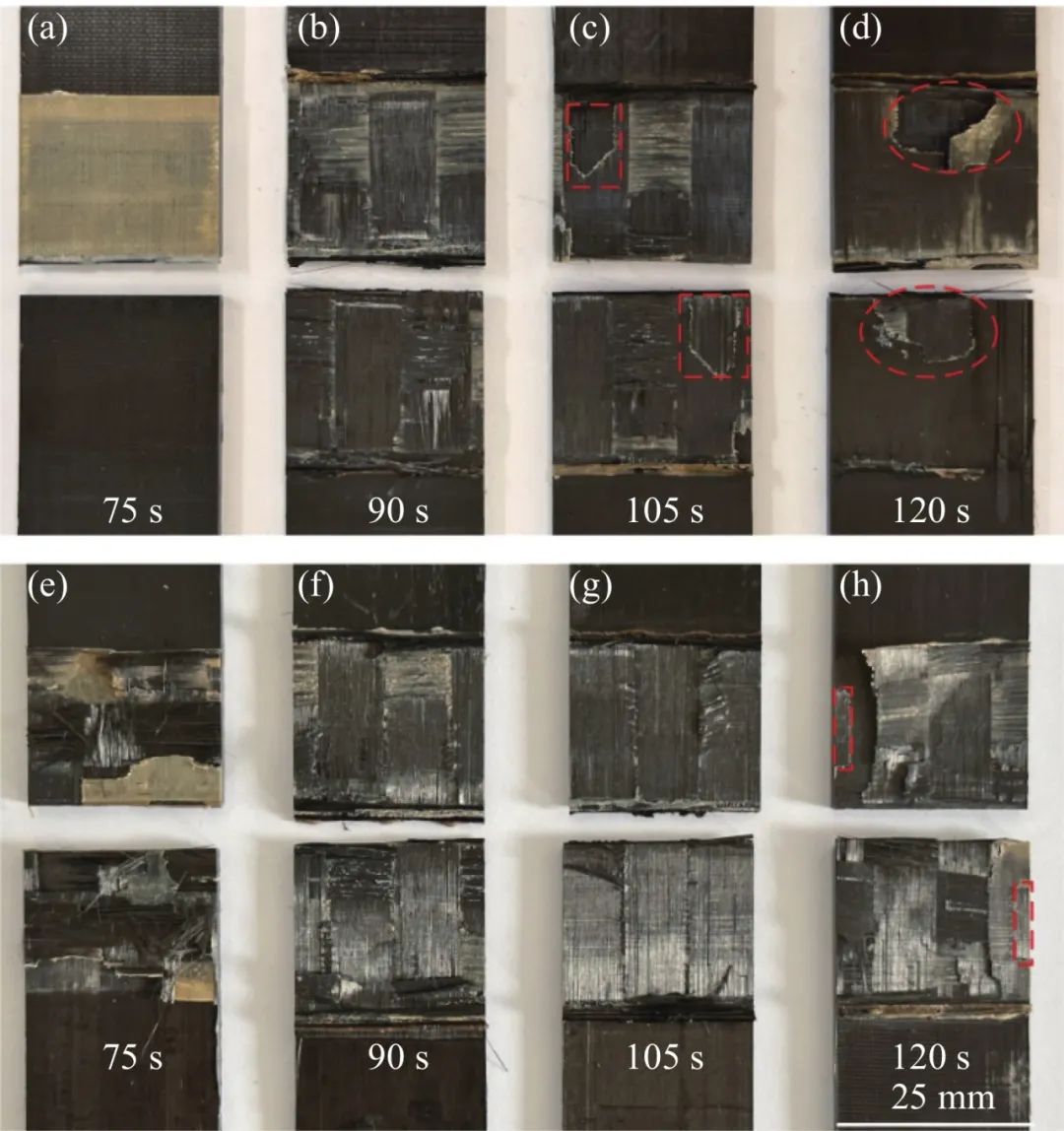
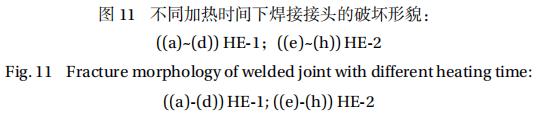
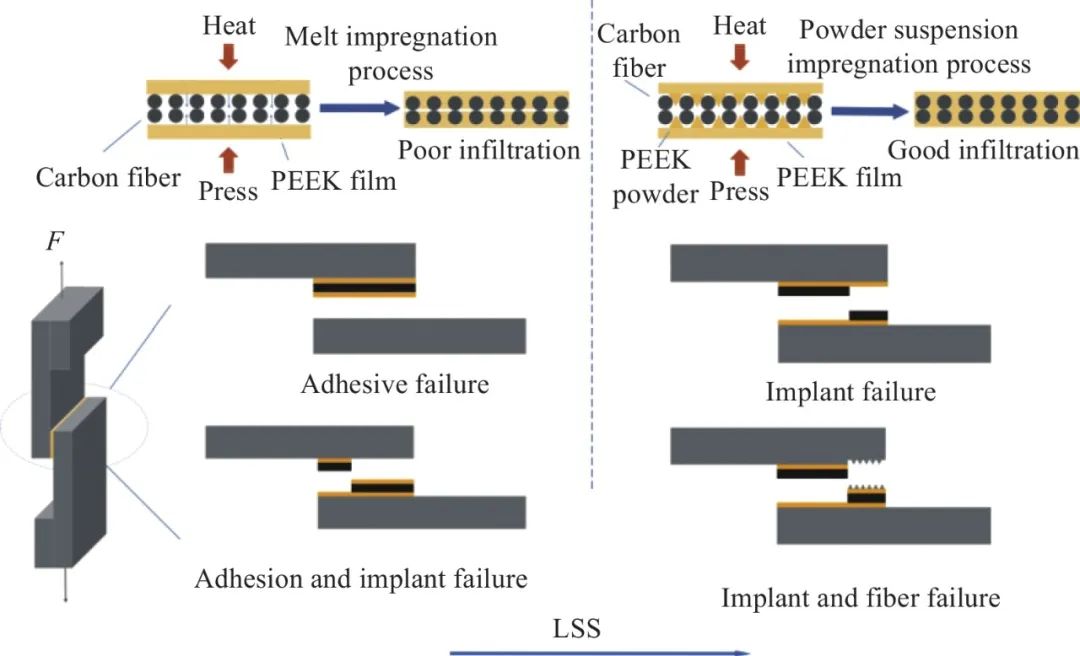
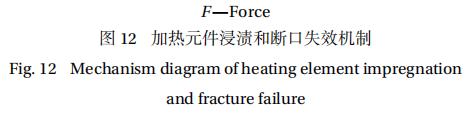
焊接界面的动态过程是评价微观断裂面的重要前提,其包括紧密接触、树脂熔融浸渍、冷却固结3个过程[26]。当加热时间较短时,界面处树脂熔融效果并不明显,焊接接头表现为粘接、植入体失效的模式,说明聚合物基体/母材之间的界面及聚合物基体/加热元件内部纤维之间的界面强度并不高。通过SEM分析断口可以发现,聚合物基体中存在孔洞(图13(a))是导致纤维/聚合物基体和聚合物基体/加热元件粘附性差的一个重要因素;由于树脂未充分浸渍,存在裸露的纤维、界面附着力弱的现象(图13(b))及加热元件接触母材表面的痕迹(图13(c)),以上现象表明该失效模式接头强度较弱。
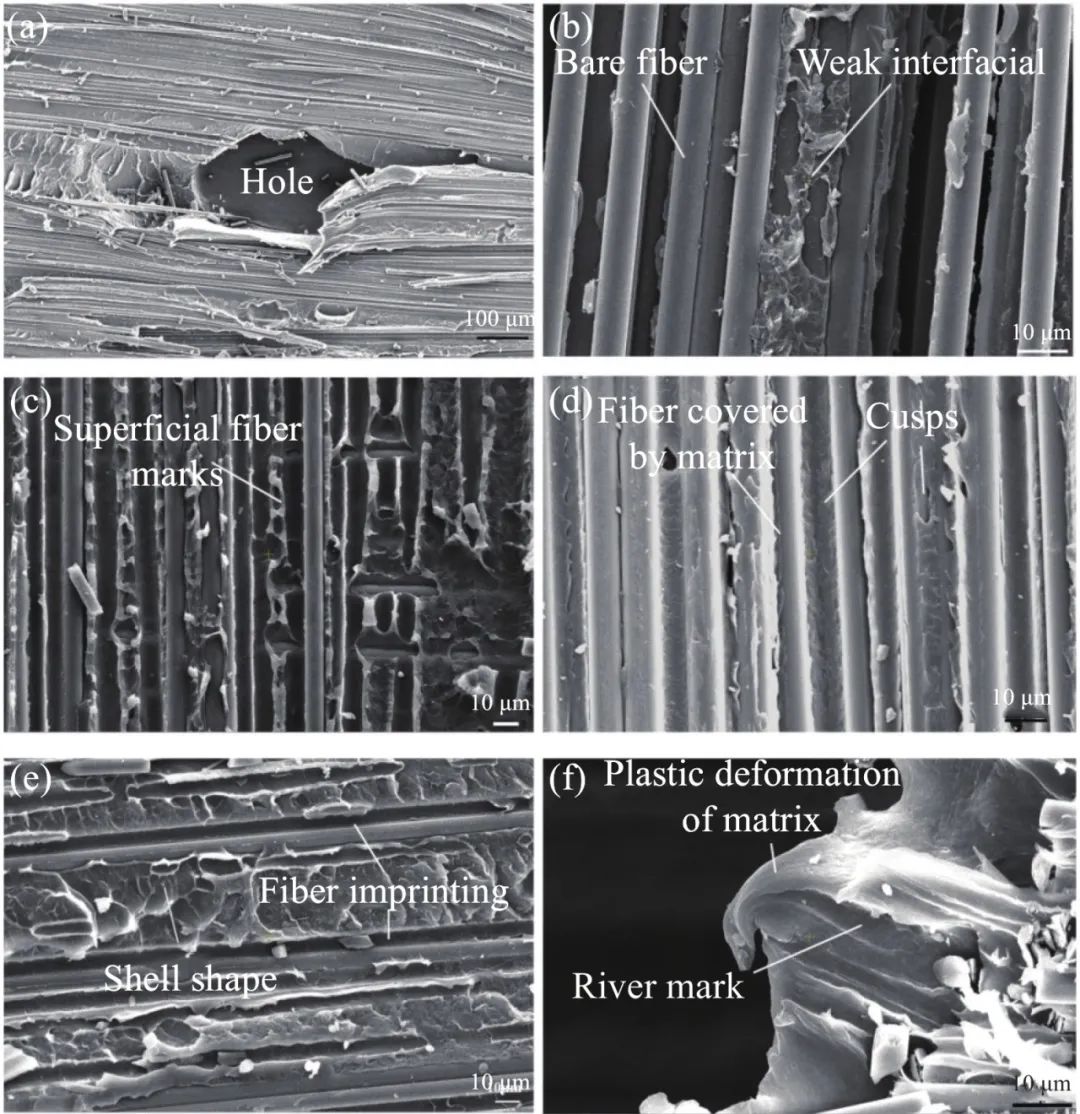

随着加热时间的增加,界面处树脂充分熔融并扩散缠结,聚合物基体与母材之间的界面结合强度提高,树脂对纤维浸渍效果明显提升,接头断口呈现出纤维撕脱及加热元件撕裂的现象,通过SEM分析断口微观形貌可以发现纤维间剪切尖峰的存在(图13(d))、纤维拔出的痕迹和贝壳形貌(图13(e))及聚合物基体的塑性变形、河流纹(图13(f)),以上现象表明该失效模式具有较高的接头强度。
3. 结 论
(1)通过粉末悬浮浸渍工艺改善了加热元件在制备过程中树脂对纤维浸渍效果差的情况,并结合熔融浸渍工艺制备了一种浸润良好的薄层碳纤维展宽布加热元件HE-1,与熔融浸渍工艺制备的加热元件HE-2相比,加热元件内部孔隙率减少,浸润性提高。
(2)在电阻焊接过程中采用“埋入式”电极的布置方式,有效避免了焊接过程中加热元件电极部分裸露而产生的“边缘效应”现象,另外绝缘层的加入避免了焊接过程中的漏电现象,并且降低了待焊接母材表面的温度。
(3)单搭接剪切强度(LSS)结果表明,不同加热元件焊接接头LSS随加热时间先增加后减小,并在120 s时达到最大值28.1 MPa (HE-1)、23.7 MPa (HE-2),结合SEM分析断口微观形貌发现LSS提升主要是由于延长加热时间后树脂对纤维浸润性提升,形成了较强的界面结合。
(4)在相同焊接工艺条件下,粉末悬浮浸渍工艺制备的加热元件焊接接头强度相比熔融浸渍工艺制备的加热元件提升15%以上,结合焊接接头截面金相及断口形貌分析发现,加热元件浸润性是影响接头剪切强度的重要因素。
参考文献
[1]周典瑞, 高亮, 霍红宇, 等. 热塑性树脂基复合材料用碳纤维上浆剂研究进展[J]. 复合材料学报, 2020, 37(8): 1785-1795.
ZHOU Dianrui, GAO Liang, HUO Hongyu, et al. Research progress of carbon fiber sizing agents for thermoplastic composites[J]. Acta Materiae Compositae Sinica, 2020, 37(8): 1785-1795(in Chinese).
[2]高亮, 贾伟, 石峰晖, 等. 反气相色谱法测定聚醚醚酮的表面性质及在提升热塑性复合材料层间性能中的应用[J]. 复合材料学报, 2023, 40(5): 2587-2597.
GAO Liang, JIA Wei, SHI Fenghui, et al. Surface characterization of polyether-ether-ketone by inverse gas chromatography and the application in the improvement of thermoplastic composites interlaminar performance[J]. Acta Materiae Compositae Sinica, 2023, 40(5): 2587-2597 (in Chinese).
[3]马全胜, 李俊含, 田思戗. 热塑性复合材料的成型工艺及其在航空器中的应用[J]. 化工新型材料, 2022, 50(6): 263-266, 271.
MA Quansheng, LI Junhan, TIAN Siqiang. Forming technology of thermoplastic composite its application in aircraft[J]. New Chemical Materials, 2022, 50(6): 263-266, 271(in Chinese).
[4]GALLAGHER E A, LAMORINIERE S, MCGARRY P. Multi-axial damage and failure of medical grade carbon fibre reinforced PEEK laminates: Experimental testing and computational modelling[J]. Journal of the Mechanical Behavior of Biomedical Materials, 2018, 82: 154-167.doi: 10.1016/j.jmbbm.2018.03.015
[5]张婷. 高性能热塑性复合材料在大型客机结构件上的应用[J]. 航空制造技术, 2013(15): 32-35.
ZHANG Ting. Applications of high performance thermoplastic composites for commercial airplane structural component[J]. Aeronautical Manufacturing Technology, 2013(15): 32-35(in Chinese).
[6]肇研, 刘寒松. 连续纤维增强高性能热塑性树脂基复合材料的制备与应用[J]. 材料工程, 2020, 48(8): 49-61.
ZHAO Yan, LIU Hansong. Preparation and application of continuous fiber reinforced high-performance thermoplastic composites[J]. Journal of Materials Engineering, 2020, 48(8): 49-61(in Chinese).
[7]BENGU Y Z B A, ESRA D, FAHRETTIN O. Review of thermoplastic composites in aerospace industry[J]. International Journal on Engineering Technologies and Informatics, 2022, 3(1): 1-6.
[8]STAVROV D, BERSEE H E N. Resistance welding of thermoplastic composites - An overview[J]. Composites Part A-Applied Science and Manufacturing, 2005, 36(1): 39-54.doi: 10.1016/S1359-835X(04)00182-4
[9]AHMED T, STAVROV D, BERSEE H, et al. Induction welding of thermoplastic composites—An overview[J]. Composites Part A: Applied Science and Manufacturing, 2006, 37(10): 1638-1651.doi: 10.1016/j.compositesa.2005.10.009
[10]LI H J, CHEN C, YI R X, et al. Ultrasonic welding of fiber-reinforced thermoplastic composites: A review[J]. International Journal of Advanced Manufacturing Technology, 2022, 120(1-2): 29-57.doi: 10.1007/s00170-022-08753-9
[11]HAQUE M S, MOEED K, ZAKA M Z. Laser welding of thermoplastics–A review[J]. Materials Today: Proceedings, 2022, 64: 1479-1485.doi: 10.1016/j.matpr.2022.04.900
[12]王飞云, 罗杰帮, 张平则, 等. 碳纤维感应元件厚度对碳纤维增强热塑性复合材料感应焊接接头力学性能及断裂形式的影响[J]. 复合材料学报, 2023, 40(4): 2405-2414.
WANG Feiyun, LUO Jiebang, ZHANG Pingze, et al. Effect of thickness of carbon fiber susceptor on mechanical property and fracture mode of carbon fiber reinforced thermoplastic composite induction welded joint[J]. Acta Materiae Compositae Sinica, 2023, 40(4): 2405-2414(in Chinese).
[13]杨苑铎, 李洋, 李一昂, 等. 碳纤维增强热塑性复合材料超声波焊接研究进展[J]. 机械工程学报, 2021, 57(22): 130-156.doi: 10.3901/JME.2021.22.130
YANG Yuanduo, LI Yang, LI Yi'ang, et al. Advances in ultrasonic welding of carbon fiber reinforced thermoplastic composites[J]. Journal of Mechanical Engineering, 2021, 57(22): 130-156(in Chinese).doi: 10.3901/JME.2021.22.130
[14]焦俊科, 徐纪豪, 井成虎, 等. 碳纤维增强热塑性复合材料/钛合金激光焊接模拟仿真研究[J]. 航空制造技术, 2022, 65(21): 45-53.
JIAO Junke, XU Jihao, JING Chenghu, et al. Numerical simulation of laser welding of carbon fiber reinforced thermoplastic composites and titanium alloy[J]. Aeronautical Manufacturing Technology, 2022, 65(21): 45-53(in Chinese).
[15]OFFRINGA A. New thermoplastic composite design concepts and their automated manufacture: Aeronautics[J]. JEC Composites, 2010, 58: 45-49.
[16]GINGER G. Thermoplastic composite demonstrators-EU roadmap for future airframes [EB/OL]. (2018-01-29) [2023-10-12]. https://www.compositesworld.com/news/Thermoplastic composite demonstrators — EU roadmap for future airframes | Composites World.
[17]WEI D L, GU Y Z, ZHU H R, et al. Influence of electrical heating metal mesh and power density on resistance welding of carbon fiber/PEEK composite[J]. Polymers, 2022, 14(13): 2563.
[18]GONZALEZ I, SANZ A, FERNANDEZ A. Characterization of metal heating elements for resistance welding of thermoplastic matrix composites (PEEK) [C]//Proceedings of the 5th Manufacturing Engineering Society International Conference (MESIC). Zaragoza: SPAIN, 2013.
[19]ROHART V, LEBEL L L, DUBE M. Improved adhesion between stainless steel heating element and PPS polymer in resistance welding of thermoplastic composites[J]. Composites Part B: Engineering, 2020, 188: 107876.doi: 10.1016/j.compositesb.2020.107876
[20]LI X K, SUN M C, SONG J P, et al. Enhanced adhesion between PEEK and stainless-steel mesh in resistance welding of CF/PEEK composites by various surface treatments[J]. High Performance Polymers, 2021, 33(8): 892-904.doi: 10.1177/09540083211001115
[21]ROHART V, LEBEL L L, DUBE M. Effects of environmental conditions on the lap shear strength of resistance-welded carbon fibre/thermoplastic composite joints[J]. Composites Part B: Engineering, 2020, 198: 108239.doi: 10.1016/j.compositesb.2020.108239
[22]AGEORGES C, YE L, HOU M. Experimental investigation of the resistance welding for thermoplastic-matrix composites. Part I: Heating element and heat transfer[J]. Composites Science and Technology, 2000, 60(7): 1027-1039.doi: 10.1016/S0266-3538(00)00005-1
[23]AGEORGES C, YE L, MAI Y W, et al. Characteristics of resistance welding of lap shear coupons: Part II. Consolidation[J]. Composites Part A: Applied Science and Manufacturing, 1998, 29(8): 911-919.doi: 10.1016/S1359-835X(98)00023-2
[24]路鹏程, 陈栋, 王志平. 碳纤维/聚苯硫醚热塑性复合材料电阻焊接工艺[J]. 复合材料学报, 2020, 37(5): 1041-1048.
LU Pengcheng, CHEN Dong, WANG Zhiping. Resistance welding technology of carbon fiber/polyphenylene sulfide thermoplastic composites[J]. Acta Materiae Compositae Sinica, 2020, 37(5): 1041-1048(in Chinese).
[25]ASTM International. Standard test method for lap shear adhesion for fiber reinforced plastic (FRP) bonding: ASTM D5868—01[S]. West Conshohocken: ASTM International, 2014.
[26]XIONG X H, WANG D S, WEI J, et al. Resistance welding technology of fiber reinforced polymer composites: A review[J]. Journal of Adhesion Science and Technology, 2021, 35(15): 1593-1619.doi: 10.1080/01694243.2020.1856514
上下滑动查看更多
来源:复合材料学报 2024年第6期
姚鑫, 霍红宇, 安学锋, 等. 碳纤维加热元件的制备及其对热塑性复合材料电阻焊接接头性能的影响[J]. 复合材料学报, 2024, 41(6): 2929-2937.
doi: 10.13801/j.cnki.fhclxb.20231113.004
免责声明:中国复合材料学会微信公众号发布的文章,仅用于复合材料专业知识和市场资讯的交流与分享,不用于任何商业目的。任何个人或组织若对文章版权或其内容的真实性、准确性存有疑议,请第一时间联系我们。我们将及时进行处理。
继续滑动看下一个轻触阅读原文
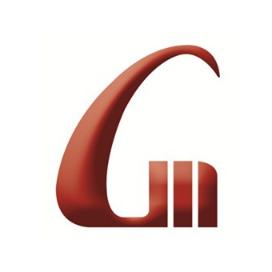
中国复合材料学会向上滑动看下一个
原标题:《【复材资讯】碳纤维加热元件的制备及其对热塑性复合材料电阻焊接接头性能的影响》
本文为澎湃号作者或机构在澎湃新闻上传并发布,仅代表该作者或机构观点,不代表澎湃新闻的观点或立场,澎湃新闻仅提供信息发布平台。申请澎湃号请用电脑访问http://renzheng.thepaper.cn。




- 报料热线: 021-962866
- 报料邮箱: news@thepaper.cn
互联网新闻信息服务许可证:31120170006
增值电信业务经营许可证:沪B2-2017116
© 2014-2024 上海东方报业有限公司