- +1
【复材资讯】SMC翼肋结构模拟
Simutence和Engenuity展示了一个虚拟过程链,可以评估过程诱导的纤维取向,从而改进复合材料翼肋的模拟结构和预测失效载荷。
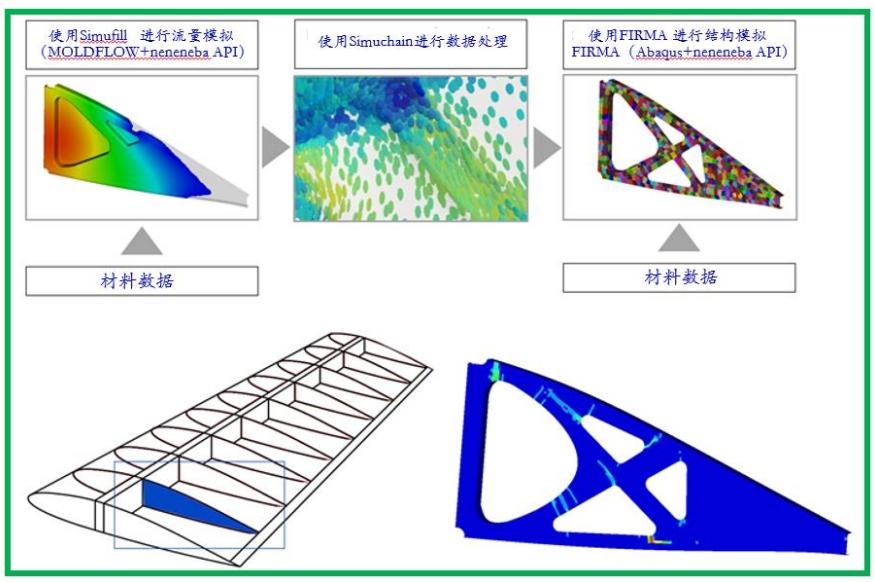
Spirit AeroSystems 参考翼肋重新设计为使用碳纤维SMC(C-SMC),展示了新 SMC 结构模拟方法的过程链。
片状模塑塑料(SMC-Sheet molding compound)是为汽车工业开发的,广泛用于中批量生产。它包括典型纤维长度约为25 毫米的短切纤维和热固性树脂。这些零件是使用压缩成型制造的,在压缩成型中,材料从其初始装 料模式流入零件几何结构。新材料的发展和碳纤维的引入将 SMC 的应用从外观和设计部件扩展到了半结构部件。
与此同时,航空航天工业正在增加产量。SMC等流程以更低的成本生产更大体积的零件是有吸引力的。然而, 由于短纤维的取向在装料流动和成型过程中发生变化, 因此难以预测最终零件中机械性能的散射,因此SMC 在更多结构零件中的使用受到限制。为了克服这一问题, Simutence(德国卡尔斯鲁厄)和Engenuity(英国西萨塞克斯)开发了一个虚拟过程链,以考虑概率结构模拟中 的过程诱导纤维取向预测。通过克服这个问题,碳纤维SMC(C-SMC)对航空航天应用越来越有吸引力。Simutence和 Engenuity 开发的方法(图 1)从使用SimuFill的高精度工艺模拟获得SMC纤维定向开始, SimuFilll是Simutence为Autodesk Moldflow软件 (Autodesk,San Rafael,California,U.S.)提供的附加 组件,Simutence还为Abaqus有限元分析(FEA)软 件(Dassault Systèmes,Vélizy Villacoublay,法国)开发了一个数据处理和映射工具插件。
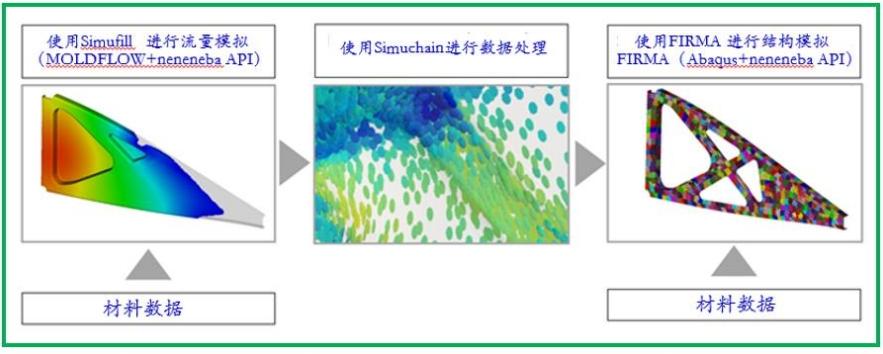
图 1. SMC 结构模拟新方法的过程链。以飞机机翼翼肋为例,模拟步骤考虑了压缩成型过程中产生的短纤维方向,然后用于有限元分析模拟。
处理后,这些数据被用于Engenuity的概率方法,称为随机材料体系结构中的失效(FiRMA- Failure in Random Material Architectures),该方法使设计师能够通过预测批次中预期的最弱和最强组件来优化SMC结构。这是通过在SimuFill流动模拟提供的分布中随机化纤维取向来实现 的,并多次运行以预测在一批部件中看到的机械性能的散射。
示范项目,材料表征
Spirit AeroSystems(英国贝尔法斯特)是一家追求新材料和制造工艺的复合材料机翼部件的一级供应商。Spirit与Simutence和Engenuity合作,选择了一个翼肋来演示FiRMA模拟方法,因为预计未来飞机将生产更 多此类零件。通过NATEP程序,FiRMA已升级为新版本FiRMA Flow,其中包括压缩成型过程中的流动效应,因此从过程模拟中得出的非随机分布用于结构模拟。
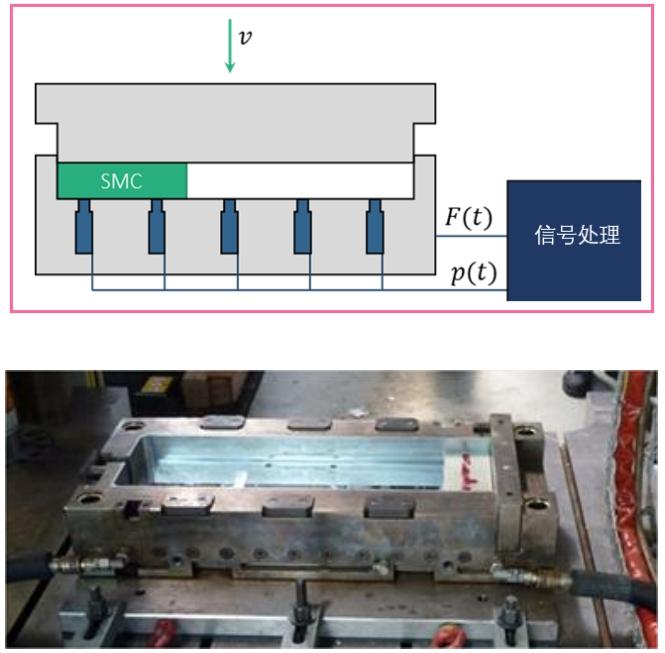
图2. SMC成型材料的特性。压缩成型试验用于为后续工艺模拟中的材料表征提供输入数据/验证。
演示者使用来自Astar(Sondika,Spain)的Carbkid VK03-5750,57 重量%的短碳纤维在乙烯基酯基质中。为了获得所有必要的材料数据,对材料进行 了工艺和结构模拟表征。对于过程模拟,SimuFill与模内表征方法一起使用(图 2),以确定变形率主导的核心区域以及模具旁边剪切率主导的润滑层的性质。在进行不同闭合速度的成型试验时,使用压力传感器和压力数据,用自动评估工具将材料参数与实验数据拟合。
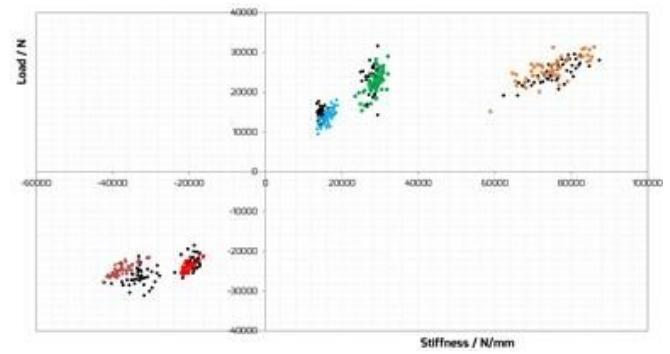
图3.材料卡的验证。这是通过比较各种样品几何形状的模拟结果(彩色点)和实验试验(黑点)来实现的。
为了表征机械性能,使用专门开发的表征程序创 建了一个具有刚度和强度数据的确定性材料卡,该程序采用了不同的试样几何形状和载荷条件。这种方法 旨在产生一种独立于规模的建模方法,并代表SMC本身所具有的负载路径冗余水平。通过迭代优化过程, 建模方法可以应用于任何规模的组件。用于材料测试的不同样品几何形状的代表性验证图如图3所示。
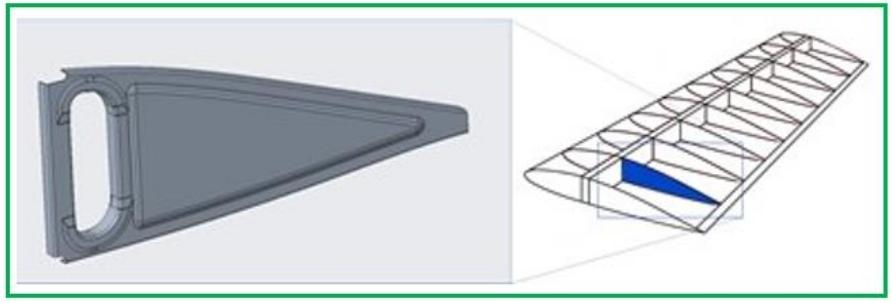
图4. 显示了机翼内的参考翼肋设计和位置。
设计定义
在为工艺和结构模拟生成了可靠的材料卡后,开始了演示机翼肋的设计。Spirit提供了参考几何形状和相应的载荷情况。额外的边界条件包括保留电缆孔/通 道的孔径以及蒙皮法兰和翼梁的尺寸。最相关的载荷情况被确定为零件固定在一侧,同时在机翼后缘向上 推动(图 4)。现有肋的设计是在临界屈曲载荷情况下进行评估的,并为SMC肋的目标提供了基准。
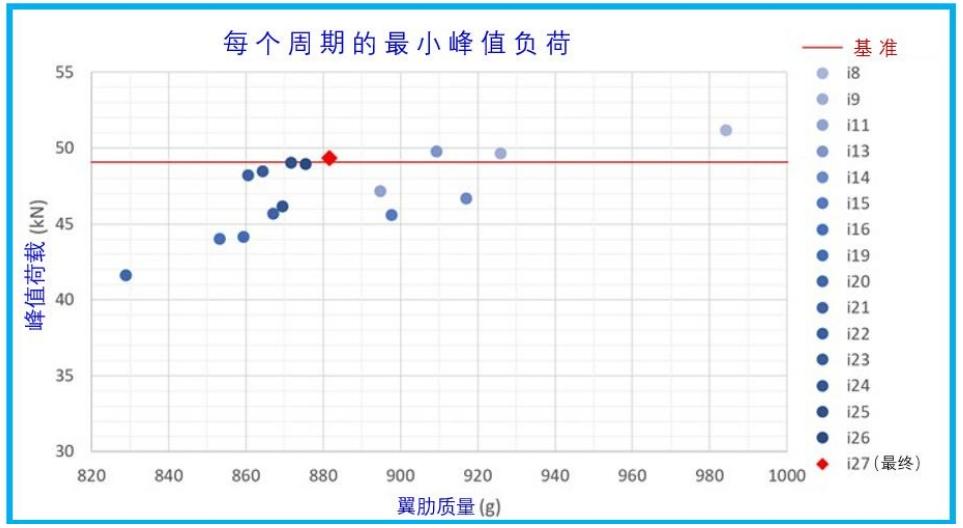
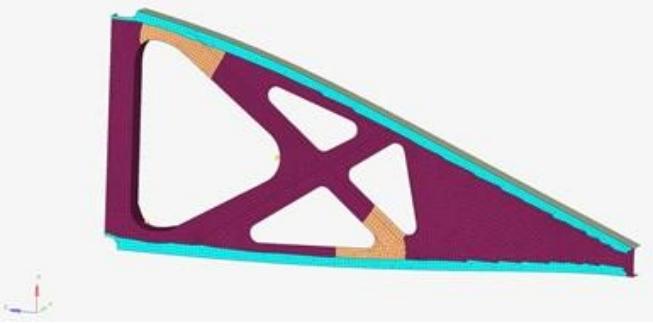
图5. 完成C-SMC翼肋设计。对设计迭代过程中的质量和最小峰值载荷的评估(顶部)导致了最终的演示器设计(底部)。
从最初的设计开始,使用FiRMA对27种设计方案进行了调查、评估和优化,以满足负载条件,同时 实现尽可能轻的重量。在这些设计循环中,进行了多个确定性结构模拟,每个模拟都按照过程模拟的指示修改了局部纤维取向,以表示实际C-SMC中的随机性程度。这导致了一系列模拟结果,但在随后的评估中 只考虑了最弱的结果(图 5)。这种基于纤维定向散射 的最坏情况确保了所有零件都能满足载荷要求的安全设计,这对航空航天应用至关重要。这种设计可以进一步优化。
过程模拟
为了提高效率,SMC成型过程模拟仅针对最终翼肋设计迭代进行。为了避免零件内出现任何焊缝,在成型后形成了这种设计的布线通孔/轻型孔。因此,成型后的零件具有封闭的表面。
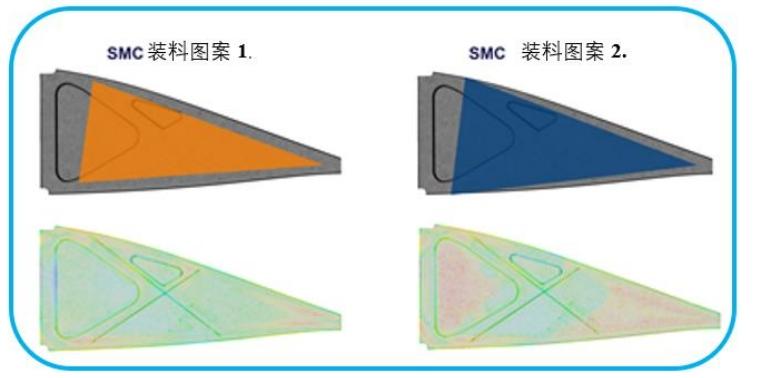
图6.装料图案的纤维方向。成型模拟中使用的最终初始SMC装料模式(顶部图像)产生了这些纤维取向(底部图像),这些纤维取向被用作Engenuity的FiRMA分析的输入。
为了确定最佳的初始装料模式,考虑了在1500毫米宽的辊上提供的C-SMC 材料的高使用率/低废料。为模拟评估了两种不同的初始装料模式。所使用的工 艺参数包括10毫米/秒的闭合速度和 200 巴的预计最大压力。通过各种优化循环,确定了这两个初始装料图案在空腔内的最佳位置,以确保零件的可制造性(图 6)。使用这两种C-SMC装料配置的模拟结果,在 Simutence的SimuChain软件的新开发模块中导出并处 理得到的纤维取向,这是图 1 所示的虚拟过程链中的第二步。然后,使用中性交换格式将结果用作新的FiRMA Flow工作流的输入。
最终虚拟验证
有了最终设计,以及来自两种不同初始装料模式 的预测纤维方向可用,可以应用FiRMA Flow工作流。对来自设计回路 27 的最终有限元模拟模型进行了修改,从而使用基于过程模拟结果的纤维取向的预测偏 差,而不是在初始设计阶段(SMC基线)中使用的一般偏差。通过这样做,产生了新的概率结果群体,然 后通过模拟散射的纤维取向和由此产生的机械性能, 有助于进一步优化装料模式及其在模腔中的位置。Spirit AeroSystems 模型转换为C-SMC肋设计,导致了图7(顶部)中所示的橙色总体分布,其中最低性 能达不到基准目标。使用自动反馈工具,如累积损伤 图(图 7,底部),它突出了50次分析运行的总体中的 所有元件故障,使设计得以改进为图 7 中的蓝色总体分布,其中预测的最小预测故障载荷(50000相对39000牛顿)将增加28%。
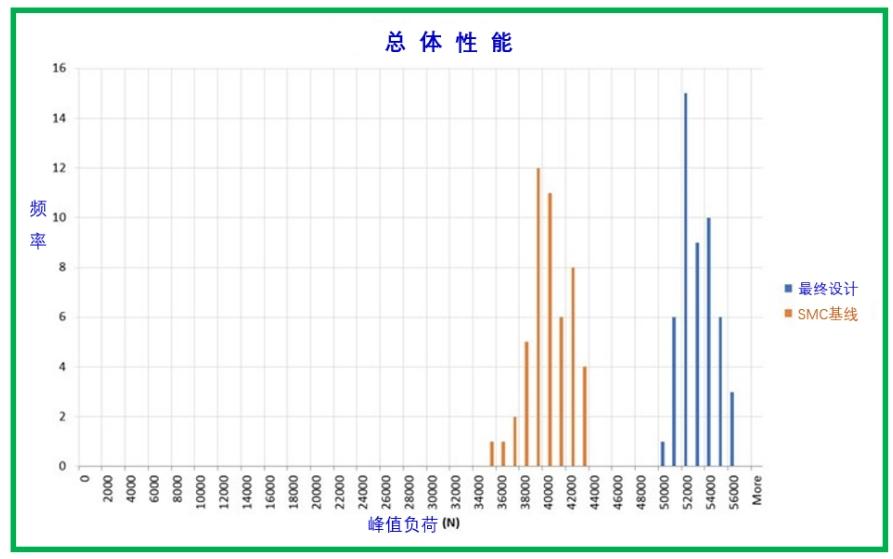
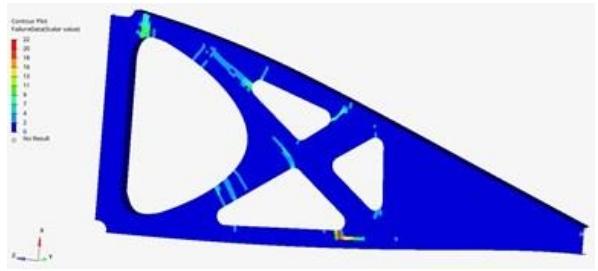
图7. 最终模拟结果。使用自动反馈工具,如50次分析的累积损伤图(底部),可以改进最初的C-SMC肋设计(顶部为橙色)(顶部为蓝色),最小预测失效载荷增加28%(50000牛顿相对39000牛顿)。
根据Simutence进行的工艺模拟,累积损伤图由C-SMC设计引起的纤维方向的所有变化产生。该图可以帮助 设计师通过必要时修改这些区域来改进C-SMC设计。这里展示的方法不仅仅是预测一个一次性的结果,而是预测一组比历史分析方法更具代表性的结果,这应该会增强安全系数的计算。这是关键,因为 航空航天要使用C-SMC,制造的结构部件必须具有在所需安全裕度窗口内的失效载荷。
这里描述的方法通过将 Simutence 的 Abaqus 有限元分析软件的虚拟过程链附加组件(包括热成型模拟、SMC冲压成型的填充模拟和映射到成型零件上的接口)与Engenuity的FiRMA相结合,证明了这一能力,这是一种独特的方法,可以识别组件群体中最薄弱的部分。由此产生的设计优化迭代使得能够预测模制C-SMC翼肋演示器的更准确的安全系数和失效载 荷。这种设计优化是在不需要任何原型级工具的情况下完成的,这加快了开发并降低了成本。
该项目的下一阶段是制造和测试多个肋,以进一 步验证这种分析方法。项目结果将于2024年公布,旨在证明结构SMC零件向零原型迈进了一步,减少了验证测试的需要,减少了此类开发中通常使用的迭代试错周期的数量。
注:原文见,《Improving carbon fiber SMC simulation for aerospace parts》2023.11.17
来源:复材邦
免责声明:中国复合材料学会微信公众号发布的文章,仅用于复合材料专业知识和市场资讯的交流与分享,不用于任何商业目的。任何个人或组织若对文章版权或其内容的真实性、准确性存有疑议,请第一时间联系我们。我们将及时进行处理。
原标题:《【复材资讯】SMC翼肋结构模拟》
本文为澎湃号作者或机构在澎湃新闻上传并发布,仅代表该作者或机构观点,不代表澎湃新闻的观点或立场,澎湃新闻仅提供信息发布平台。申请澎湃号请用电脑访问http://renzheng.thepaper.cn。





- 报料热线: 021-962866
- 报料邮箱: news@thepaper.cn
互联网新闻信息服务许可证:31120170006
增值电信业务经营许可证:沪B2-2017116
© 2014-2024 上海东方报业有限公司