- +1
文科毕业的我,在小工厂做管理
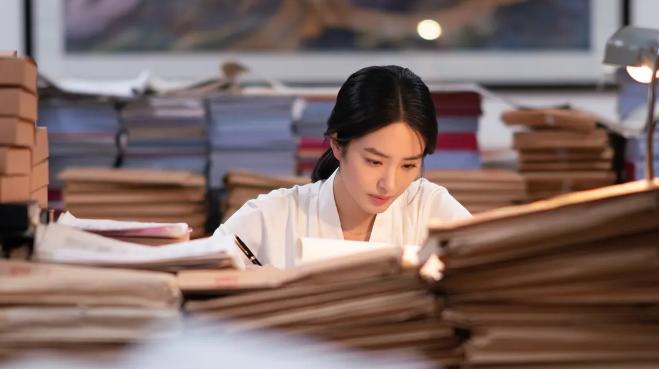
- 职 业 故 事 -
人生就像一段长途旅行,在不同时节看不同的风景,在不同阶段学不同的技能。希望自己可以继续保持相对较高的不可替代性,在将来有权力主动选择留下或离开。
自大学毕业后我从事过电商客服、运营、人事行政、新媒体运营等各种工作,也与朋友合伙开过两家公司,但生产管理是真的不曾想过。在我看来,做生产一定要懂技术,而我所知的电路电子相关知识,都仅限于中学的物理课堂。
工作终还是要做的,何况沈总对我抱了太大期望,他坚信以我的“沉稳细致、聪明好学”,一定可以很快胜任。于是在我对新公司熟悉了三个月后的12月中旬,沈总一张机票回了欧洲,要与家人共度圣诞和新年,把刚创立半年的小工厂甩给了我。
“不用怕,放心大胆做,有什么解决不了的问题就给我打电话。”他又补充,“工程技术相关的事情也可以找林总。”
林总是公司另一位股东,与其他合伙人还经营着一家方案公司。他本人其实也不太懂技术,但在行业内日积月累总会耳濡目染了解一些,最重要的是他有人脉,许多问题都可以从朋友那里寻求到解决方案。只是,林总的身影在工厂一个月也难见一次。
唯一慰藉的是我们工厂甚小,只一条流水线简单组装产品,然后质检、包装即可。所谓的组装,就是把方案商提供的PCBA焊接上重要的传感器等小插件,然后与外壳、液晶屏、背光板、锂电池(如果需要)等通过卡扣或螺丝按流程组合到一起,再贴上保护镜片质检后就可以包装出货。
因公司刚成立不久,仅有六款量产仪器。产线单一,操作流程简单,所以年初的两个月,工厂一切都很顺利。我趁这段时间,一边在网上找资料学习生产管理,一边到车间熟悉生产工艺。收获最大的是看维修员检修不良品,慢慢的我可以自己判断一些故障原因,比如屏幕断字是因为斑马条松动,屏幕重影是因为电压过高,数据显示--是因为传感器模块接触不良等。
产品第一次出问题是从终端客户那边发现的。当时我们C01型家用检测仪刚上市三个月左右,在国内电商平台极为畅销,且好评如潮。但随着夏季到来,客服开始陆续收到一些买家对质量问题的负面反馈,主要原因是产品外观有破损。起初偶尔有一个,后来每周都会有两三个,多为仪器镜片右下角出现磨损或开裂。
我与车间主管仔细查看后,一致认为是快递运输途中抛卸货物所致。为减少这类货损,我们把包装盒中的防震泡棉又多加了两层。先试装了20台仪器,并对每个包装做了10次以上的抛落测试,之后拆开检查确认产品全都完好,才放心地安排仓库以后按新的包装方式发货。
本以为万事大吉,结果客服部仍会不断收到投诉,且随着气温升高,投诉也日益增多。但根据之前的经验判断,这绝对不可能是运输造成的损坏了。盯着退回的那些仪器,我甚为头疼,难不成这镜片质量还受温度影响?
让维修员把破损的镜片更换上新的,为方便观察,我把更换后的产品全摆在了自己办公桌上。结果静置三天后发现,其中一个镜片静悄悄地自己裂了……我惊出一身冷汗,火速跑去仓库,连拆了3箱180台仪器,果然不少产品都出现了同样问题。清点后发现数量竟多达13台,7%的不良率!
我马上安排品管把所有库存重新质检,而我与车间主管则把坏的镜片一一拆除,又拆了几台良品,多次交叉对比后终于找到原因:尺寸不合。具体来说是因气温升高,小部分镜片与胶壳热胀冷缩后接触位置过挤,时间一久便挤爆了。我用卡尺测了镜片和胶壳尺寸,与资料库数据对比后发现,两款配件大小都有误差,且镜片是正误差,胶壳为负误差,组装后可不就要挤爆了……
通常来讲,有经验的师傅在开模具生产前,就会考虑到不同材料的热胀冷缩系数以及生产误差,避免大货时出现配件过挤无法组装或组装后缝隙过大的情况。现在意外发生,我只得与注塑厂和镜片厂沟通解决方案。
于我而言,无论是胶壳扩大还是镜片改小都可解决问题,但于供货商而言,他们则需要付出额外成本去修改模具。一番拉锯战后,最终成本相对较小的镜片厂做出让步,加急按小尺寸重新出图纸开模生产。一周后新镜片到货,这个问题才得以解决。
镜片生产尺寸过大本是供方责任,但在沟通中我发现自己技巧不足,无法让对方心甘情愿承担全部损失,又害怕态度过于强硬影响后续新产品打样时效,向沈总请示后最终双方各承担一半。
后来这款产品又出过一个新问题:客户使用几个月后镜片会自动脱落。为此我们给一个台湾客户前后免费发了三台仪器(前两台仪器使用一段时间后镜片都自动脱落了,而退换货又因关税加运费成本过高不划算)。
起初我推断是镜片背胶粘性不足,但与供货商确认后得知我们所有产品镜片都用3M公司的同一款双面胶,其他产品却从未出现过这种情况,只得又从胶壳方面找原因。拿了样品仔细对比,发现这批胶壳贴镜片位置表面竟然做了纹理,与外壳表面的纹理一模一样!虽漂亮,但表面不平整会造成贴胶后空气渗入,时间一久,胶被风干或腐蚀失去粘性,镜片自然会脱落。联系塑胶厂质问原因,对方才告知之前模具被工人不小心损坏,再次晒纹时没留意多晒了一部分,承诺会尽快把这部分模具重新修整好,并同意我们退回带纹理的胶壳。
经此两件事后,我觉得仓库验收配件过于敷衍,于是重新制订了验收货物的流程,要求不止要核对配件的名称、规格型号、数量、外观等,还要实际装机测试效果与功能,有异常情况及时提报。
除了内销,我们也有少量外贸订单,其中出货较多的是一款电波钟。因之前为我们提供这款产品PCBA的台湾公司报价上涨过多,我们决定更换供货商。在深圳实地考察了四五家做此类方案的企业后,最终选定了Y公司。
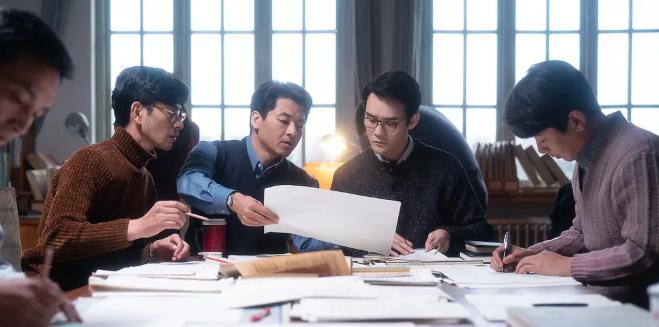
样机及产品功能、按键定义发给对方一个月后,我们拿到了Y公司发来的PCBA样品,但测试结果并不理想,闹铃音乐效果较差,功能方面也有小问题。收到反馈,Y公司对程序重新做了调整,但闹铃音效仍不够好。思来想去决定使用我们之前的音乐IC。Y公司拿到IC样品与规格书后一周左右,发来最终的PCBA样品。测试效果完美!
但在所有配件齐全,可以批量生产时,却发现新组装的两台大货样机喇叭不能发声。我们先更换了喇叭重新测试仍无声音,又把这两个喇叭装在早期产品上,结果可以正常响铃。我只得再次联系Y公司工程师,并把两台样机快递过去。几天后对方回信息说是程序问题,大货使用的是我们客供音乐IC,而他们烧录的却是老程序。最后对方派了两名员工,带着手动烧录设备,坐在我们产线的最前端,花了四天半时间去更新10K的主板程序。
在车间忙着生产这批电波钟时,仪表行业内开始流传一个交期50天、数量200K的二氧化碳检测仪大单。调查后得知,大约20天前,日本政府突然下发了一份文件,要求公共场所配备二氧化碳检测仪,通过监测二氧化碳浓度监控人流,从而降低新冠肺炎感染风险。
之前这类仪器属于小众产品,全球需求量都不大,厂家数量也少。结合当时芯片供应情况、二氧化碳模块厂家及几家仪表龙头企业产能分析,我们认为当时无一家公司可单独拿下此订单。于是沈总当即决定:“用最快的速度开发这款产品!即使分不到这块大蛋糕,但只要速度够快,三个月内能抓到一些贸易公司的散单,咱们也有不少利润!”
立项当天,沈总、林总与我三人加班到晚上11点半,终于把产品功能、按键规划定义完成。次日一早,林总便到方案公司进行程序软件设计沟通。我负责编写说明书,同时联系第三方机构确认产品上市销售及出口日本需要做的各项检测认证时间及费用。而沈总则亲自到设计公司盯外观设计,且另付了加急费,在当晚10点多时拿到了三款设计文件,39小时后拿到3D打印的手板。之后半小时内我们选定了鲨鱼脊设计那款外观,再由沈总联系工程师做结构设计。
设计文件一到手,沈总马上拉了新项目群,方案公司陈工、结构堆叠设计杨工、PCB厂程工、液晶屏厂谭工、塑胶厂秦工等,加上我和林总共12人。之后的四五天全是大家对各种配件尺寸规格的讨论与协调。
期间我还要与平面设计同事完成屏幕显示效果图,再发给液晶屏厂去出菲林图,最后确认图纸及各项数据、走线没问题后安排打样。同时,沈总跟进塑胶厂对外壳部分进行开模及打样。林总跟进PCB的设计、打样及BOM表完善。哪个部分出现卡顿,我们便会直接杀到对方公司盯着解决问题。记得胶壳第一次出来的样品组装后侧面拼接缝隙上下不均匀,沈总、我和秦工一直在模具厂车间呆到凌晨一点多,直到最后问题解决才离开。
通常一款电子产品从立项到最后出样机,至少要2个月时间,而我们只用了39天!之后又用10天时间完成了产品的各项检测认证。至此,这款产品已经可以安排量产。经此一事,我对深圳、东莞企业的高效有了新的认识,也对沈总的果断与雷厉风行甚为佩服。
安排车间加急生产了200台产品,给近一个月内询单的所有企业都发去样品及报价,最终收获了七个客户,其中四个客户在之后的一年半内多次返单,赢利占到我们疫情期间全公司利润的70%,总算是抓住了这波红利的尾巴。
在我们开发产品期间,其他企业的库存早被抢空,甚至连之后一两个月的产能都已被包销。我深刻感受到信息差的价值,于是之后开始学着关注一些政策新闻。
此前经常听业内朋友感慨日企对产品细节如何吹毛求疵,我的真实体验便是来自于这批合作客户中的两家企业。
其一是日本PIN公司,当时的联系人是夏野先生。因疫情原因客户不便到东莞验厂,所以在下单前的沟通会更加仔细慎重。夏野先生前后验收过两次样品,并对质检的每个流程都进行了视频确认,而首单却只订了6箱216PCS。为了确保对方满意,我们特意多做了一遍质检。货物发佐川急便的航空快递,五天后到达客户公司。
隔日夏野先生便联系我,先微笑着肯定了我们的高效,之后又带点遗憾地说产品细节方面稍有不足,并发来一个9秒的视频。视频中仪器屏幕在光照下被缓慢地旋转了360度,某个角度时镜片右上角闪现出一个极微小的浅灰色颗粒物。
之后夏野先生又发来一份正式的“不良の報告”。他说:“我知道这个粉尘在正常查看仪器数据时不会被看到,但万一,我是说万一,有客户对产品爱不释手仔细观察,你知道的,这个小瑕疵会让客户很失望。对这个产品,对我们企业,对你们工厂,都很失望。我希望以后的货物不会再出现这种情况。”为解决这个问题我们不得不重新安装了一间手术级无尘车间。
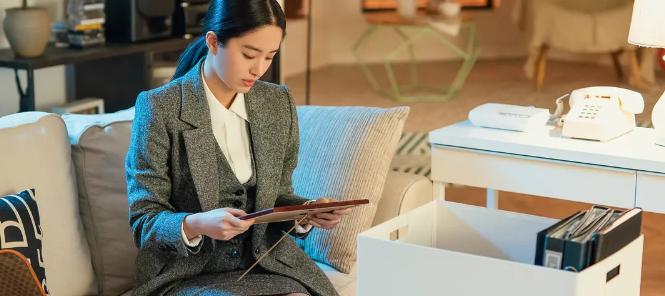
之后的合作中夏野先生又反馈过各种细节问题,比如某批货中有一台仪器的USB接口插线时手感稍有卡顿,某批货部分包装盒侧面有一道压痕,以及有一箱货中两个产品摆放与其他产品方向不一致等。在此之前,因从未有客户(包括欧洲客户)提及这些,我也不曾留意。夏野先生的反馈,让我意识到,在重视产品的功能和质量之外,也应对各种细节有更高要求。
在与PIN公司合作期间,我所有的加班几乎都是在与夏野先生沟通细节问题。他的细致、耐心、执着,以及责任感,都让我印象深刻,值得学习。哦,对了,还有感谢他中文非常棒,让我们可以毫无障碍地交流。
另一个客户是我们通过台湾NOAH国际间接合作的日企S公司。NOAH主要提供产品支援服务,协助S公司在中国大陆进行采购。从疫情期间到我司实地验厂、产品功能程序定制设计、样品确认及出厂前验货,到包装时说明书摆放方向、条形码粘贴位置等细节,对方要求所有事务都要按流程操作,并且每一项都必须有书面文件,任何调整也都要及时更新相应文件,哪怕只是外箱唛头位置上移1cm。
因公司刚成立一年多,又在疫情期间,缺乏专业人才,车间及仓库都是员工根据经验管理。这就造成NOAH专员第一次来验厂时发现了非常多的问题,比如PCB板没有做真空保护,工具没有贴编号,物料卡不齐全,电子料未全放静电盒内,镙丝刀无扭力管控等。我拿着笔记本跟在专员身后一项项做记录,极为尴尬,感觉我们工厂连个街边小作坊都不如。
专员现场做好报告提交后告诉我验厂结果不太理想,但好在给了二次验厂的机会。之后一周,我与仓管和车间主管逐条排查,购买相应物料,到认识的朋友工厂学习,对照报告一一整改。NOAH专员通过视频二次验厂后终于通知我们合格。经此事后,我再面对其他公司的验厂专员时,变得相当有底气。
之后终于进入到产品部分。因为功能、丝印LOGO及包装全要重新设计,样品又需发台湾NOAH与日本S公司分别确认,真正下大货订单时已是3个月之后。期间各种的SOP文件加起来有近30份,每次按客户要求完成这款产品的一份SOP时,我就按同样标准把我们其他产品也整理一份。待NOAH要求的文件全部完成时,我们工厂的各项流程制度文件也全部完善好,管理相应也得到极大提升。
在管理工厂的两年间,总会遇到各种问题,关于产品、客户或者管理。哪里有问题,我便去向哪里,我感觉自己就像一块万能的砖,哪里需要哪里搬。但在寻求问题原因与解决方法的过程中,又有许多趣味,并能学到新知识。这些知识让我不断进步,慢慢可以不动声色地解决各种问题。
最近公司有意向转型做亚马逊,于是我又开始突破现在的舒适圈,加紧学习亚马逊店铺运营知识。人生就像一段长途旅行,在不同时节看不同的风景,在不同阶段学不同的技能。希望自己可以继续保持相对较高的不可替代性,在将来有权力主动选择留下或离开。
我一直坚信,沉下心来磨炼自己,永远比仰望别人更有意义。
原标题:《文科毕业的我,在小工厂做管理》
本文为澎湃号作者或机构在澎湃新闻上传并发布,仅代表该作者或机构观点,不代表澎湃新闻的观点或立场,澎湃新闻仅提供信息发布平台。申请澎湃号请用电脑访问http://renzheng.thepaper.cn。





- 报料热线: 021-962866
- 报料邮箱: news@thepaper.cn
互联网新闻信息服务许可证:31120170006
增值电信业务经营许可证:沪B2-2017116
© 2014-2024 上海东方报业有限公司