- +1
产业竞争力报告⑦中国重型燃气轮机产业长期滞后,如何攻关
燃气轮机是一种复杂而先进的成套动力机械设备,它是继蒸汽轮机、内燃机之后出现的新一代动力装置,也是迄今为止热-功转换效率最高的发电类动力装备。作为高新技术集聚的典型产品,它是关系国防安全、能源安全、保持工业竞争力的战略性装备,一定程度上集中体现了一个国家的科技水平、综合国力和重工业水平,是装备制造业“皇冠上的明珠”。
一、中国重型燃气轮机的竞争力现状
尽管中国现已具备轻型燃机(功率5万千瓦以下)自主化能力(只是具备技术能力,尚未正式推向商用市场),但重型燃气轮机(功率5万千瓦以上)仍基本依赖进口。长期以来,重型燃气轮机设计、制造、试验等尖端技术完全垄断于德国西门子(SIEMENS)、美国通用电气(GE)、日本三菱(MHI)等少数公司,目前国内重型燃气轮机尚未完全掌握重型燃气轮机热端部件制造、维修以及控制等尖端技术,也并未形成系统全面的研发、设计、试验与维保体系,与上述国际重型燃气轮机先进企业相比差距在30年以上。中国重型燃气轮机尚有许多关键核心技术有待突破,燃气发电技术装备存在较大瓶颈,重型燃气轮机设计、制造、调试、运维等多领域均存在被“卡脖子”的风险。
1、德美日少数企业垄断了重型燃气轮机先进技术
一般来说,燃气轮机涡轮前能够承受的温度越高,技术等级越高,性能也越先进。根据涡轮前温度和压比,重型燃气轮机通常可分为E级、F级和H级。目前全球最先进的一代重型燃气轮机,分别是美国通用电气研制的H级和日本三菱日立研制的J级。除此之外,市场主流的重型燃机是E级、F级,全球也仅有少数公司能生产这类高水平的燃气轮机。总体来看,目前世界上完全具备重型燃机研制能力仅有五家企业:美国通用电气(GE)、德国西门子(SIEMENS)、日本三菱(MHI)属于第一梯队,上述三家公司均具备成熟的E、F级重型燃气轮机技术,同时最先进的H、J级产品也已研发完成开始进入市场;法国阿尔斯通(目前已被GE收购)和意大利安萨尔多(2014年被上海电气集团收购)属于第二梯队,当前也具备成熟的F级重型燃机设计制造能力。目前中国重型燃气轮机主力机型为引进并国产化制造的F级和E级燃气轮机,但E级/F级燃气轮机关键核心技术仍被美国通用电气、德国西门子和日本三菱日立公司所垄断。目前中国国内尚无建成并投入运营的H/J级燃气轮机项目,2019年上海电气和安萨尔多合建的H级重型燃气轮机应是中国首台H级重型燃气轮机。值得一提的是,韩国斗山重工在2020年获得了首个重型燃机订单,从而成为继德国西门子、美国通用电气、日本三菱和意大利安萨尔多之后的第五个先进燃气轮机OEM厂商。
2、中国重型燃气轮机仍存在被“卡脖子”的风险
目前,中国国内重型燃气轮机主机制造企业,主要以上海电气、东方电气、哈尔滨电气等几家合资合作企业为主,上述国内燃机制造商大都只拥有部分(冷端部件和整机组装)制造技术,尚没有完全独立自主的核心研发能力,并没有形成完整的自主可控的重型燃气轮机产业体系。
2001-2007年6年间,中国由哈气-美国通用、东气-三菱重工、上气-西门子、南气-美国通用等4个联合体引进了E级和F级重型燃气轮机60余套共2000万千瓦。通过这一过程,国内四大重型燃气轮机制造企业掌握了E级和F级重型燃气轮机的冷端部件制造和整机组装技术,但是核心的设计和热端部件制造技术仍然为外方所垄断,不得不主要依赖进口。从重型燃气轮机关键核心部件国产化进展来看,以市场主流的F级重型燃气轮机为例,目前中国重型燃气轮机生产与制造技术国产化率大幅提高,中国燃气轮机零部件数量国产化率可达到80%-90%,但燃气轮机零部件价值的国产化比重还不到70%。
直到2019年,中国重燃才完成F级300MW燃机第一级动叶、静叶和燃烧室的制造,东方电气集团首台F级50MW重型燃气轮机原型机整机点火试验成功,才表明中国突破了一系列“卡脖子”关键核心技术,初步获得了重型燃机高温部件制造技术能力,初步具备了自主研制E级/F级重型燃机的全过程能力。
燃气轮机关键零部件国产化程度
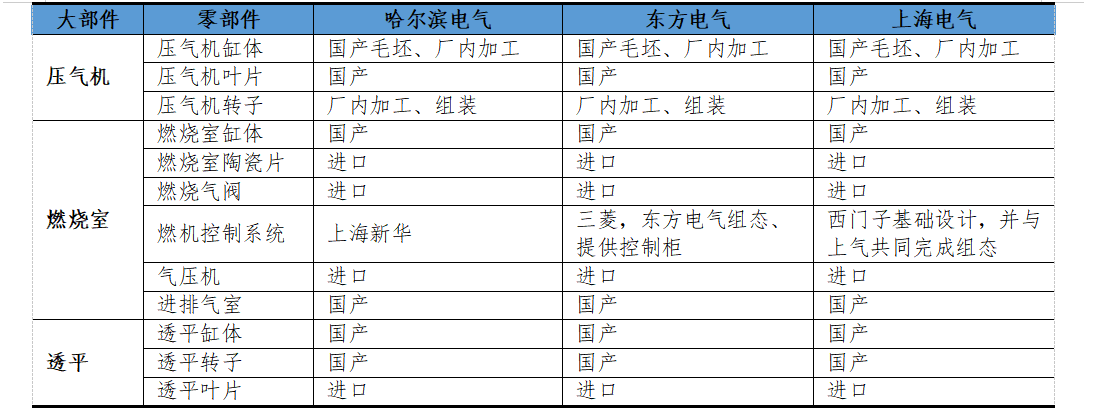
资料来源:作者根据各公司官网、广发证券报告等收集整理。
3、新时代中国重型燃气轮机自主创新发展进入快车道
2010年以后,随着国内重型燃气轮机市场的快速增长,中国重型燃气轮机产业进入发展快车道。
一是继续通过与国际垄断巨头合作,学习引进国际先进重型燃气轮机技术。2014年,上海电气入股意大利安萨尔多,使中国有能力初步实现E、F级重型燃机国产化,这是中国重型燃气轮机跨越式发展的关键一步。
二是以2012年党中央国务院启动“航空发动机与燃气轮机”国家科技重大专项(下称“两机专项”)为标志,中国利用新型举国体制开展重型燃气轮机自主研发设计。2014年9月,中国联合重型燃气轮机技术有限公司(下称“中国重燃”)在上海挂牌成立,它是承担国家重型燃气轮机重大专项的新型科研企业,主要承担重型燃气轮机型号和工程验证机研制、关键技术研究与验证等科研工程项目等任务。2017年,为加快推进燃气轮机产业创新发展与关键核心技术国产化替代,国家发展改革委和国家能源局联合发布了《依托能源工程推进燃气轮机创新发展的若干意见》,依托哈尔滨电气、东方电气、上海电气、中国航发、中国船舶重工集团等10家单位组织了第一批燃气轮机创新发展示范项目。2018年教育部批准清华大学协同中国重燃成立“燃气轮机省部共建协同创新中心”,以国家“两机专项”中燃气轮机研制需求为导向,开展燃气轮机科技攻关研究和应用基础研究。2020年6月“中国燃气轮机产业创新联盟”正式成立,创新联盟由中国重燃担任理事长单位,集聚了国内高校院所、创新中心、动力集团、制造企业和行业用户等66家燃气轮机产学研用领域的核心单位,初步构建了研发设计、制造试验和运行维护相结合的高效合作机制。
中国重型燃气轮机产业链存在的主要问题
当前,中国重型燃气轮机产业链存在的问题主要体现在三个方面:一是燃气轮机研究、设计、试验等基础设施建设长期滞后,二是燃气轮机技术涉及的众多基础科学和学科基础较为薄弱,三是传统“市场换技术”燃气轮机发展路径难以持续。
1、燃气轮机研究、设计、试验等基础设施建设长期滞后
重型燃气轮机开发需要完整的设计、制造和实验体系,中国燃气轮机研究、设计、试验等基础设施建设在历史上长期处于落后状态,总体上与世界先进水平的差距非常大。在燃气轮机应用基础研究试验设施方面,2000年之前国家投入主要集中于各大学和科研院所,相关基础设施建设总体呈现投资少、水平低、多重复、小规模等特征,且各大学与研究机构基础研究实验设施多以小型、低参数的机理性设备为主,彼此间独立自发建设,缺乏协调和沟通,普遍存在利用率不高和设施浪费问题。
综合来看,当前中国重型燃气轮机研究、设计、试验设施装置仍然较为缺乏且不成体系,尚没有形成重型燃气轮机“应用基础研究-关键技术验证-产品研发设计-部件性能试验验证-生产制造”全产业链完整的试验设施平台体系。
2、燃气轮机技术涉及的众多基础科学和学科基础较为薄弱
燃气轮机技术属于高科技产品,涉及材料学、空气动力学、燃烧学、传热学、工程热力学、自动控制技术、先进制造技术等多种学科。由于中国众多基础科学和学科基础薄弱,一定程度上导致了中国重型燃气轮机整体质量与效能的落后。
虽然中国较早提出了国际公认的叶轮机械三元流动理论(科学家吴仲华于20世纪50年代提出),奠定了燃气轮机设计的理论基础,但在落地技术上中国并没有及时跟进,重型燃气轮机的设计技术、制造技术与材料技术均没有真正掌握;1980年到2000年期间,中国部分高校一直在进行学院式、论文式探索,但国内大部分高校并没有设置重型燃气轮机专业,全国真正从事过重型燃机研究设计的技术人员不到两位数,重型燃气轮机攻关面临无人才储备、无技术储备、无试验设施储备的“三无”挑战,离重型燃气轮机技术应用还有相当远的距离。2012年中国设立重燃专项时,上述基础科学和学科基础薄弱问题仍然没有得到有效解决,燃气轮机研究、设计、试验、运营等一系列基础工作不够扎实,研究设计试验系统性、协同性不足,试验产出的重型燃气轮机达不到长时间高效稳定安全运营的结果及效果。
3、传统“市场换技术”燃气轮机发展路径难以持续
重型燃气轮机是典型的设计建造一体化(AE模式)产品,合资合作“市场换技术”的燃气轮机发展路径,在中国重型燃气轮机起步阶段发挥了重要积极作用,但无法在新历史发展阶段继续支撑中国重型燃气轮机迈向产业价值链、创新链高端。以前“技术引进、打捆招标”的发展方式,一方面满足了当时国内对燃气轮机电站建设的迫切需求,另一方面通过加大燃气轮机设备本地生产制造的比例,既减少了工程造价并降低了运营成本,又促进了中国重型燃气轮机生产与制造环节的国产化替代,为中国引进消化吸收国际重型燃气轮机先进生产制造技术做出了一定贡献。但在国际科技竞争日益激烈背景下,一方面国际领先企业加强对我关键核心技术的全面封锁,只有通过独立自主创新才能解决依赖进口且缺乏议价权的热端部件制造维修技术、关键备件以及控制等技术;另一方面,在与外方合作共同生产制造燃气轮机产品过程中,外方通过合作协议和专利技术等特别约定,严重限制了重型燃气轮机制造企业的技术改进和品牌创造,使得“市场换技术”的发展路径面临诸多限制制约,不利于中国燃气轮机迈向产业链高端。
构建基本完整重型燃气轮机产业链的政策建议
为弥补中国重型燃气轮机产业链的缺陷和短板,突破国际领先企业对中国燃气轮机关键核心技术的制约与封锁,进一步提升重型燃气轮机自主创新能力。当前亟须重点做好以下几方面工作。
1、充分发挥新型举国体制与市场力量协同攻关
推动重型燃气轮机国家科技重大专项和“卡脖子”工程,并不是常规意义上科研活动的自由创新,而是在国外技术封锁存在被“卡脖子”风险情况下的“后发赶超”。因此,有必要在发挥市场决定资源配置的基础上,通过新型举国体制,采取诸如“揭榜挂帅”等机制,集中力量高质量、高效率地推进实施国家重大任务。
一要充分发挥“中国燃气轮机产业创新联盟”的纽带与桥梁作用,加强国内高校院所、创新中心、动力集团、制造企业和行业用户等燃气轮机产学研用核心单位的联系沟通,协同构建项目式、矩阵型的攻关团队,形成协同高效、密切配合的工作机制,打好关键核心技术攻坚战,形成研发、设计、制造、试验、维修和应用相结合的重型燃气轮机产业协同攻关体系。
二要充分发挥中国重燃的引领协调作用,按照“小核心、大协作、专业化、开放式”要求,以“科研工程化”为引领,搭建好重型燃气轮机设计建造一体化(AE模式)协同平台,集研发、设计、安装、调试与运维等全生命周期与各环节于一体,实现研发设计的可制造性,提高重型燃气轮机产业链、创新链的整体效能。
三要更加充分发挥市场的资源优化配置决定力量。重型燃气轮机新型举国体制应坚持市场配置资源为主,关键核心技术攻关应摒弃单纯的技术挂帅思想,要兼顾注重技术路线的目标实现和注重成本效益的商业利益,以市场化应用和客户认可信任为最终目标。
2、积极开展国际合作完善自主创新体系
一要继续加强与美国通用电气、日本三菱重工、德国西门子等企业的国际合作,防止中国重型燃气轮机企业与国际“脱钩”。中国重型燃气轮机市场需求增长快速且潜力巨大,重型燃气轮机企业失去中国市场将在激烈国际竞争中落于下风,难逃失败命运。同时,新一轮科技革命和产业变革正在重塑世界,德国西门子、日本三菱重工、美国通用电气等重型燃气轮机企业正处于数字化转型起步阶段,失去中国市场将迟滞上述国际企业的转型升级。因此,尽管重型燃气轮机技术被国际少数企业垄断,但中国燃气轮机企业存在诸多有利契机,仍然可以继续与国际先进企业保持密切合作。
二要依托重型燃气轮机产业链核心单位完善中国重型燃气轮机的自主创新体系。除了加强国际合作借鉴国际经验,构建完善的产业技术创新体系和服务体系外,还要把握好智能制造、数字转型等时代契机,大力推进重型燃气轮机转型升级,积极将智能算法、增材制造技术等新兴产业技术融入重型燃气轮机设计制造一体化过程,从而为燃气轮机行业提供新的生产方式,降低设计与生产成本,不断缩短产品研发周期,大幅提高生产效率,进而逐步构建重型燃气轮机设计制造的自主创新体系。
3、释放更多政策红利促进重型燃气轮机快速发展
2012年以来,党中央国务院启动了包括“两机专项”等在内的多项支持政策,持续推动重型燃气轮机高端装备制造业发展,但目前尚没有成熟的完全自主的重型燃机产品,尚未建立自主可控、体系完整的产业链和创新体系。
一是建议国家支持政策由专项的科技政策、产业政策,适当拓展到采取财政、税收、金融、贸易等多元政策体系支持,多措并举释放更多政策红利,根据细分领域和任务设立专项基金支持,全面提升产品研制、加工制造、售后服务等体系能力建设,加快推进燃气轮机产业自主创新发展,逐步实现进口依赖的关键核心技术国产化,形成以企业为主体、产学研用相结合的具有竞争力的重型燃气轮机产业体系和自主创新技术体系。
二是建议支持采用自主知识产权重型燃气轮机发电企业的鼓励政策,继续实施好《依托能源工程推进燃气轮机创新发展的若干意见》,实施好重型燃气轮机重大专项的重点工程项目,有效扩大重型燃气轮机设计、研发等工程项目市场需求,在加快推进清洁能源生产的同时,为自主创新燃气轮机核心技术提供市场空间。
(作者胡文龙系中国社会科学院工业经济研究所副研究员、研究室副主任。本文摘自《产业蓝皮书:中国产业竞争力报告(2021)》,经作者审订,授权澎湃新闻刊发)





- 报料热线: 021-962866
- 报料邮箱: news@thepaper.cn
互联网新闻信息服务许可证:31120170006
增值电信业务经营许可证:沪B2-2017116
© 2014-2024 上海东方报业有限公司