- +1
公司主力催化裂化装置创效显著,效益创历史新高
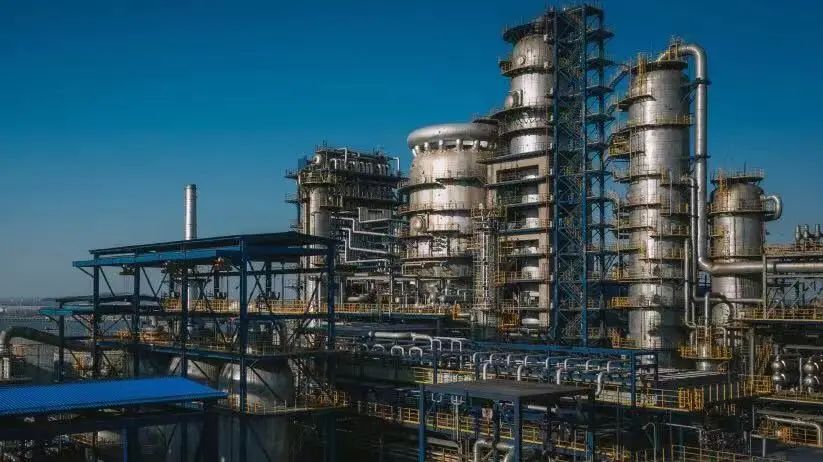
今年以来,金陵石化克服疫情等影响,紧抓市场机遇,根据市场需求,调整主力创效装置——3号催化裂化装置生产,调控产品方向、优化操作流程、开展技术改造、强化降本增效,丙烯等高附加值产品产量不断提高,截至目前,效益创历史新高。
提高丙烯收率 实现创效增效
3号催化裂化装置年处理量达350万吨,主要原料为渣油、蜡油等重质油,生产汽油的同时副产丙烯、丙烷等轻烃产品。
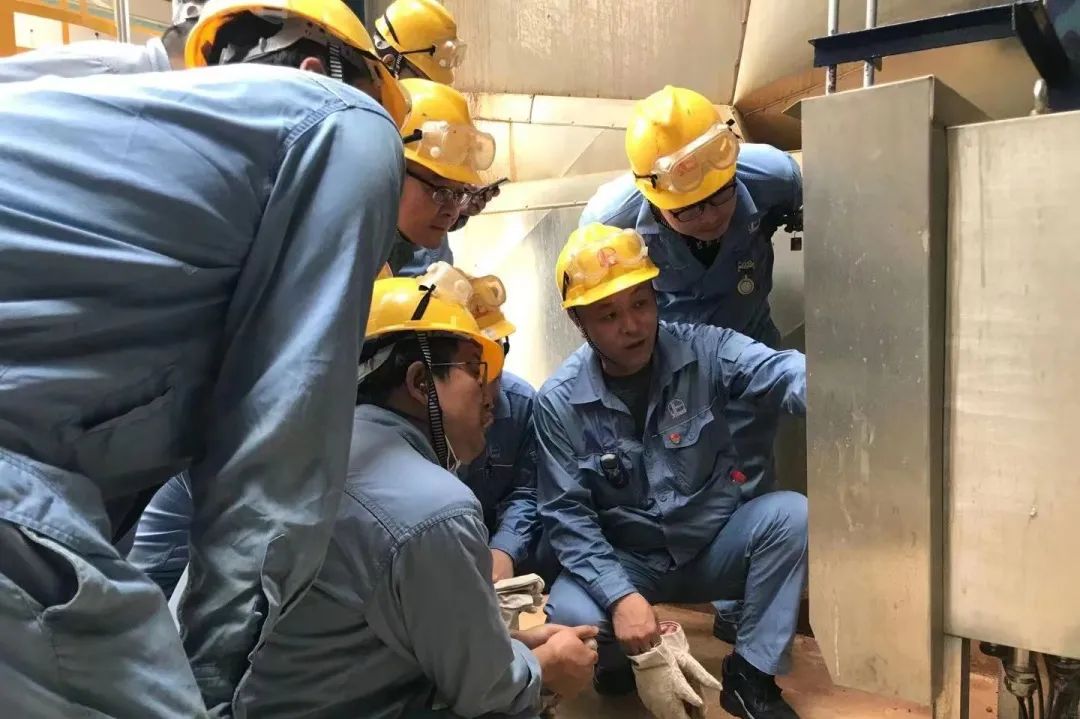
去年以来,受疫情影响,丙烯作为口罩及医用防护用品原材料,市场需求大幅增长;航班数量减少,航煤库存增加。
为增产丙烯、压减航煤,炼油四部开始回炼航煤,提高3号催化裂化装置丙烯收率,满足市场对丙烯的需求。他们制定详细的操作制度,组织开展培训,监控操作参数,合理分配产品流向,实现增产丙烯的目标。截至目前,该装置丙烯收率达6%,经济效益显著。
实施技术改造 确保安稳生产
再生器相当于3号催化裂化装置的“肝脏”,在长周期运行的情况下出现了尾燃现象,顶部温度升高,如果不及时解决会损伤其他生产设备,影响装置长周期运行。
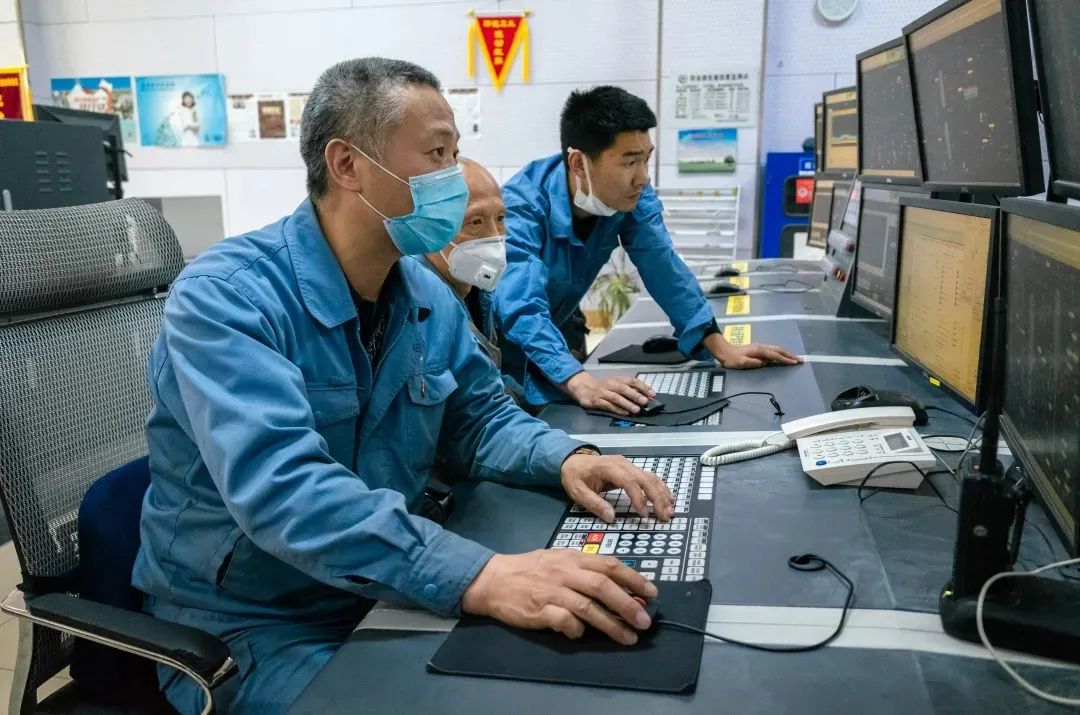
针对该问题,炼油四部成立攻关小组,在多次研讨和到外部交流学习后,找到了“清热降火”的良方。他们升级改造再生器内部,提高烧焦罐中部氧含量,使一氧化碳燃烧更完全,消除再生器尾燃现象;同时加装取热器,将多出来的热量用于生产过热蒸汽,增产中压蒸汽实现增效。
目前,装置轻重汽油分离、油浆脱固等科研攻关项目正在稳步推进,完成后将有力提高平稳生产水平和产品质量,为企业创造更多效益。
回收催化剂 实现降本
该装置的加工原料以重油为主,受原料中存在重金属成分等影响,部分催化剂失活,降低了催化剂使用效率。
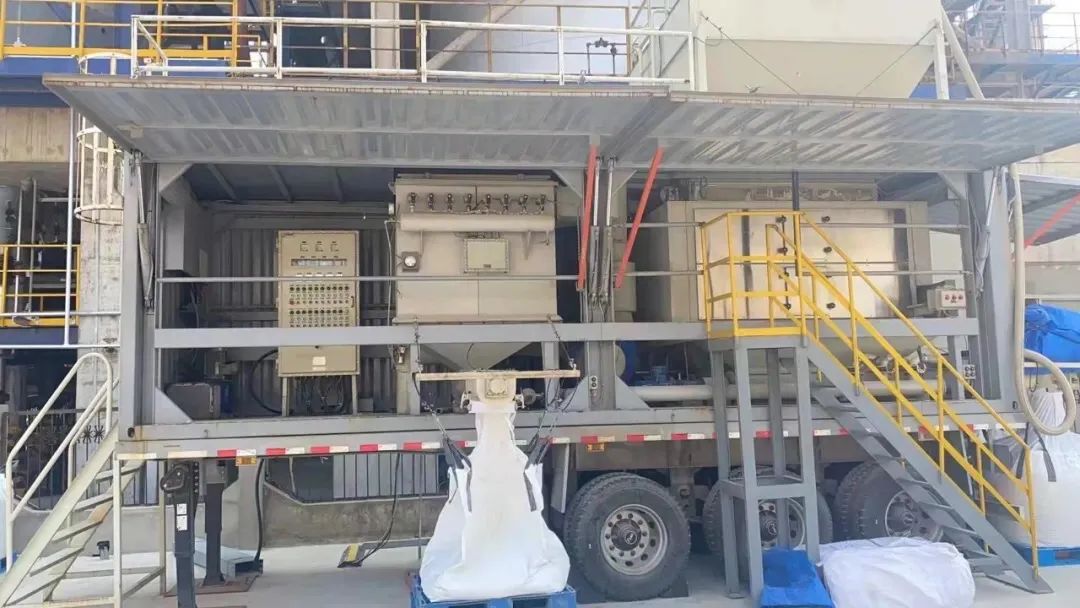
为此,炼油四部增设移动式废催化剂磁分离回收设备,将废催化剂中使用时间短、重金属含量低、仍保持较高活性和选择性的部分分离出来,送回装置使用,达到节约催化剂的目的,同时减少废催化剂处置量、降低处理成本。该技术年初应用以来,已回收低磁剂504吨,新鲜剂消耗量同比减少10%。
改造烟机 提升节能降耗水平
该装置烟机已投用8年时间,使用效率逐年下降,存在较为严重的叶片结垢现象,电机能耗明显升高。
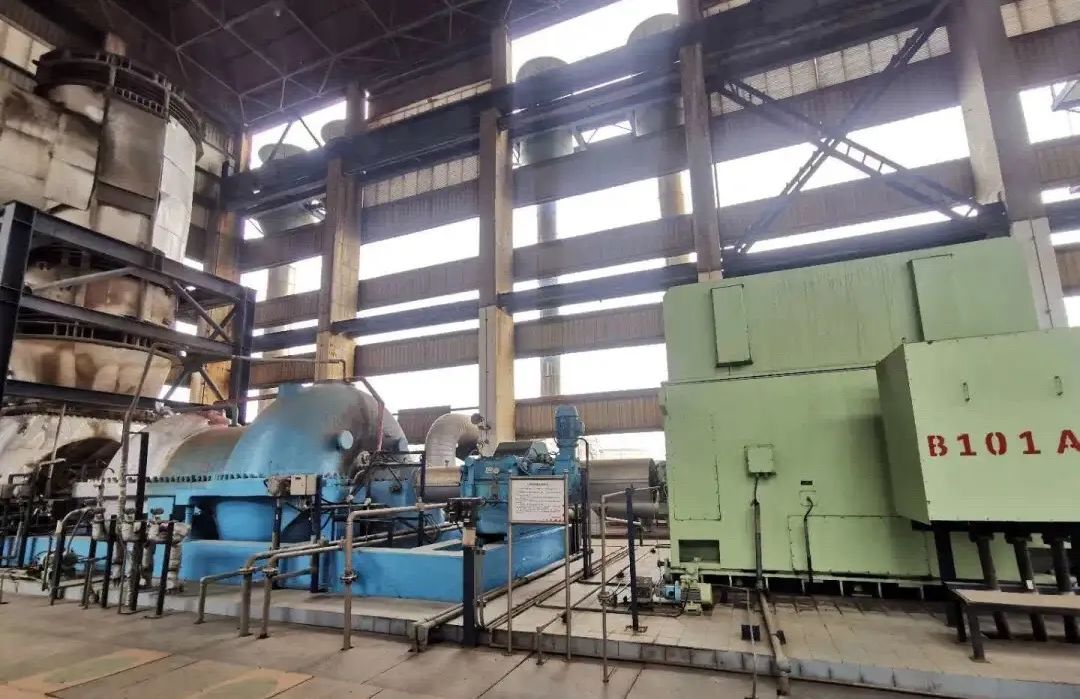
针对这种情况,相关部门成立专项攻关小组,对烟机进行节能改造,减缓气流冲蚀、减少叶片结垢,提高烟机效率。烟机改造后,在相同工况下,主电机电流大幅减小,实现节电。
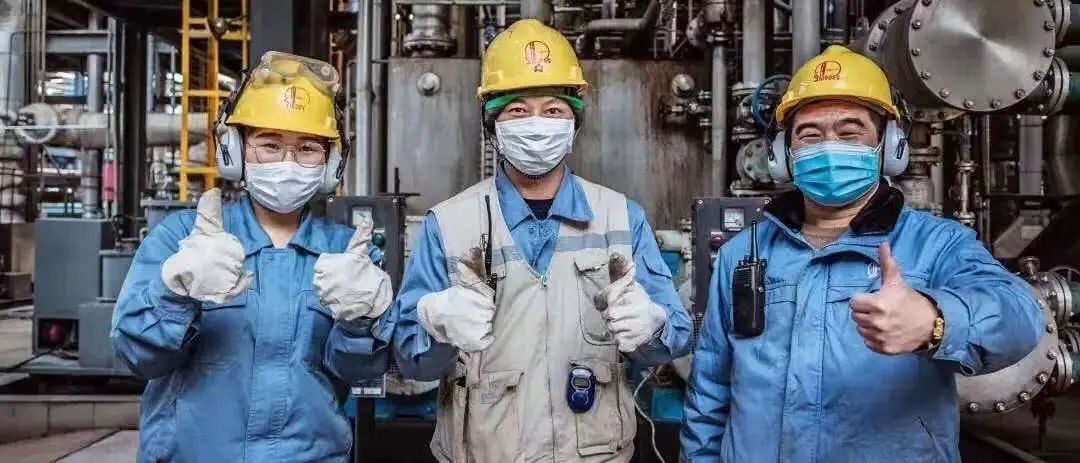
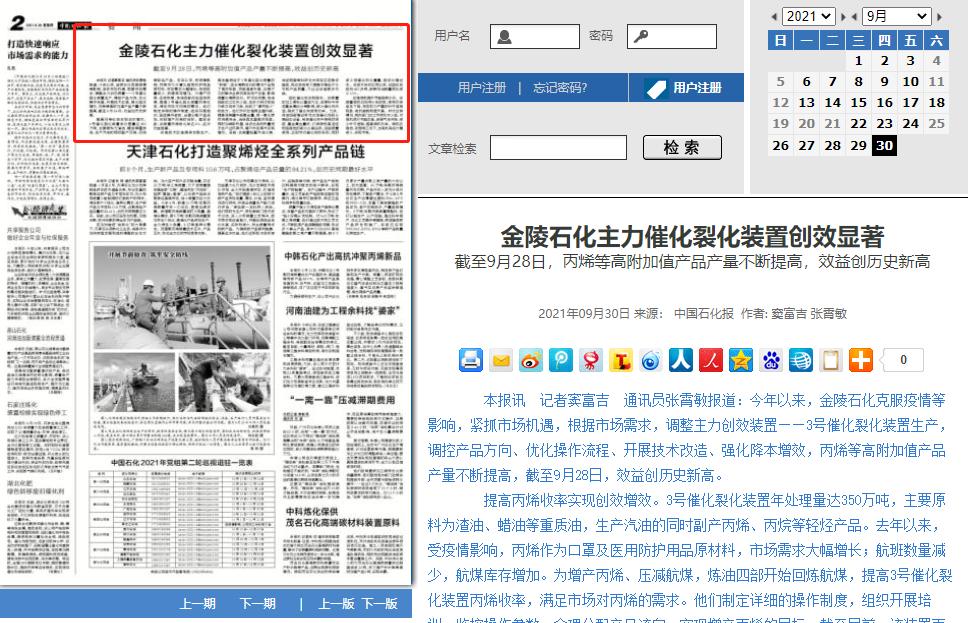
《中国石化报》2版头条报道公司主力催化装置创效成效
图、编:吕倩
文:张霄敏
校:朱 虹
2021年第683期 总2315期
原标题:《公司主力催化裂化装置创效显著,效益创历史新高》
本文为澎湃号作者或机构在澎湃新闻上传并发布,仅代表该作者或机构观点,不代表澎湃新闻的观点或立场,澎湃新闻仅提供信息发布平台。申请澎湃号请用电脑访问http://renzheng.thepaper.cn。





- 报料热线: 021-962866
- 报料邮箱: news@thepaper.cn
互联网新闻信息服务许可证:31120170006
增值电信业务经营许可证:沪B2-2017116
© 2014-2024 上海东方报业有限公司