- +1
灯塔工厂观察|数字化转型中如何将IT技术纳入工业逻辑?
从蒸汽机,到电,到信息技术,工业发展历经了机械化革命、电气化革命与信息化革命。2011年,德国提出工业4.0的概念来概括数字化与智能化带来的制造业变革。
变革的发生往往不是一夜之间的显著变化,就像15世纪的人们绝不会一天早上打开窗忽然听到 “中世纪结束”的宣言,它常常是润物细无声的。变革也是不均衡分布的,工厂是直观感受变革的一个绝佳观察地。
对于当下制造业的变革, “黑灯工厂”、“无人工厂”成为关注焦点,其因机器对人彻底替代的极致性而变成观看变革的窗口。但这并不是当下存在最普遍的情况,也并非是制造业变革的方向目标。
实际上,从工业逻辑出发,不可忽视的两个关键词是良品率与成本——尽可能提高良品率与尽可能降低成本。当然,当下而言还要增加“绿色”和“低碳”。
那么具体而言,数字化转型中如何将IT技术纳入工业逻辑,让数字化转型安全及“看得见”成效?
“在与亚马逊云科技的合作中,我们构建了云-边协同AI工业视觉检测平台,实现了产品质量缺陷的智能检测,将检测误检率降到0.5%内,漏检率降为0%,实现全自动和智能化,”在施耐德电气武汉的发展中“灯塔工厂”,施耐德电气全球供应链中国区数字化解决方案负责人冒飞飞分享道。
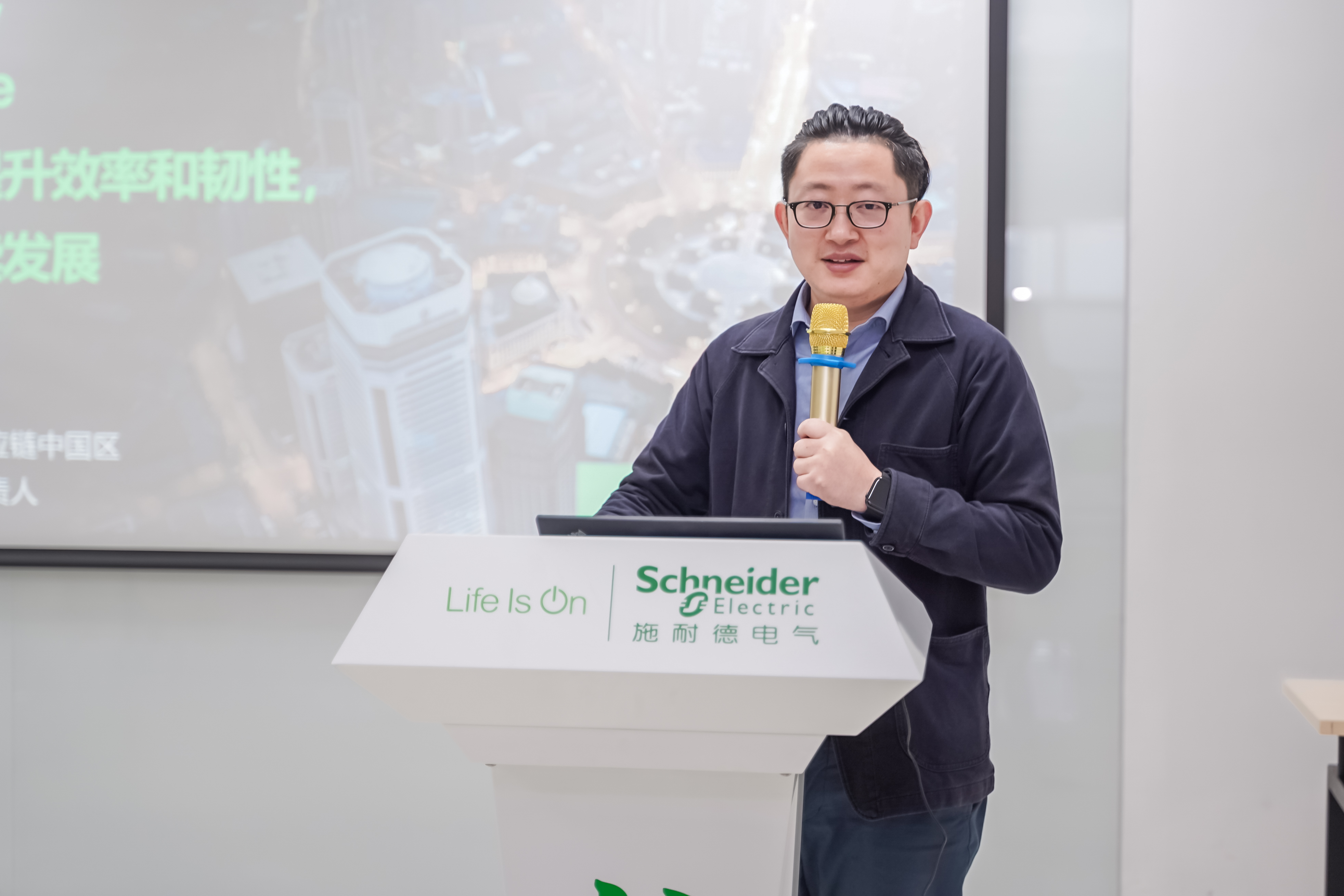
施耐德电气全球供应链中国区数字化解决方案负责人 冒飞飞
施耐德电气武汉工厂在2018年被达沃斯经济论坛和麦肯锡从全球工厂中选出,评为发展中的“灯塔工厂”,同年11月被国家工信部评为“绿色工厂”,主要生产微型断路器、接触器和其他工业控制类的小元器件,这三类产品的产能目前在施耐德电气所有工厂中是第一。
施耐德电气武汉工厂是施耐德电气全球28家工厂中第一家全面部署EcoStruxure整体解决方案的工厂,在两年时间内完成了楼宇、配电、机器、工厂、电网五大系统的智能化、物联网升级改造。工厂里有348个无线电能测量模块,传感器实时监测着压力、温度、湿度等,能源使用被及时适应性调控,机器设备可以在出现故障前就被及时干预,最后实现了0配电故障停机,以及超过10%的能源优化。
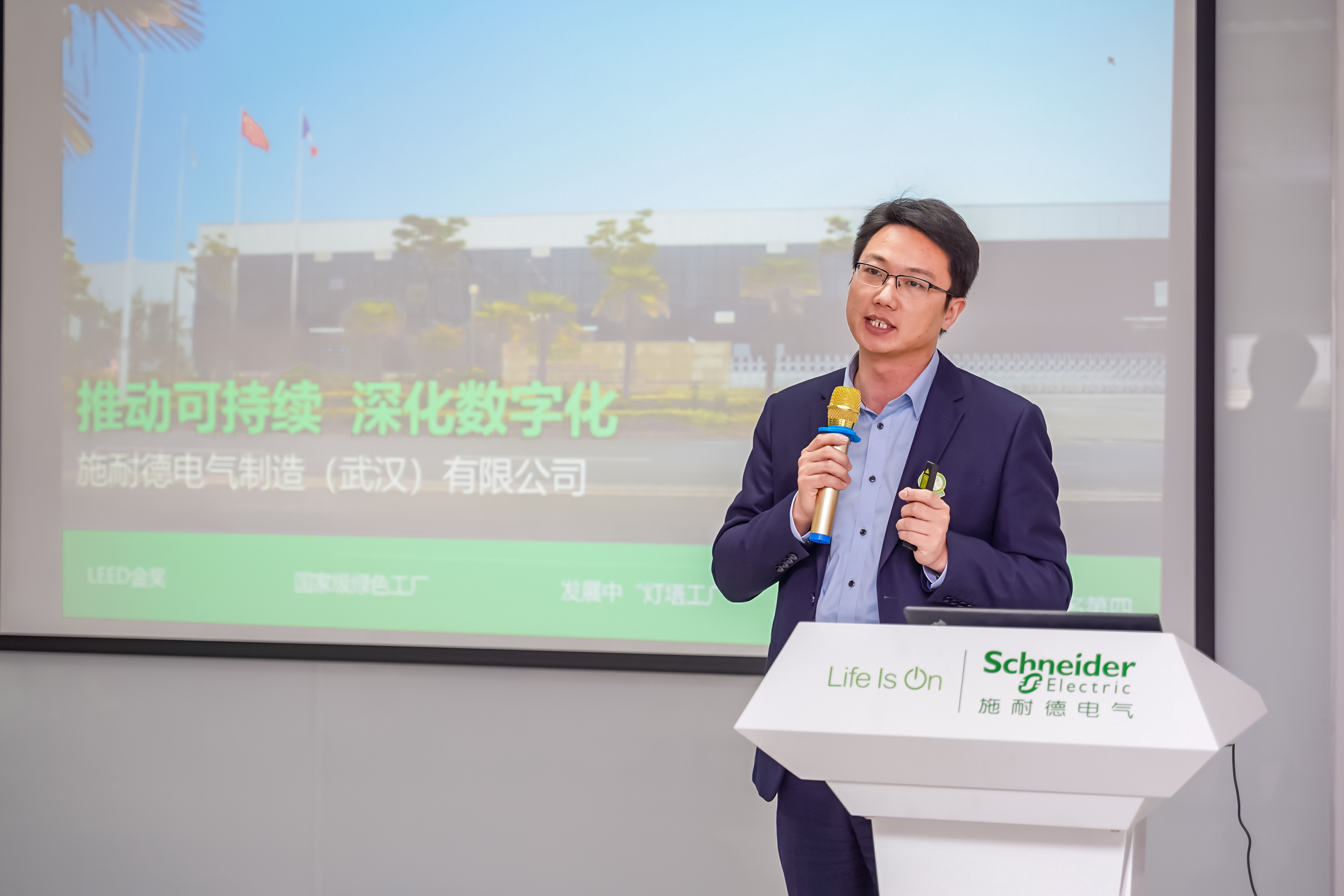
施耐德电气制造(武汉)有限公司总经理 李聪
“武汉这家工厂的发展历程可以简单归结为三个部分,第一部分是不断提升内功,提高公司在精益生产和精益运营方面的能力。第二部分是加速自动化的升级改造,第三部分是数字化的转型,”施耐德电气制造(武汉)有限公司总经理李聪表示。
冒飞飞则阐述了实现数字化的四维融合,“一是能源+自动化,二是从终端到云,三是从设计与建造,到运营和维护,四是从分散式管理到集成化企业管理。”
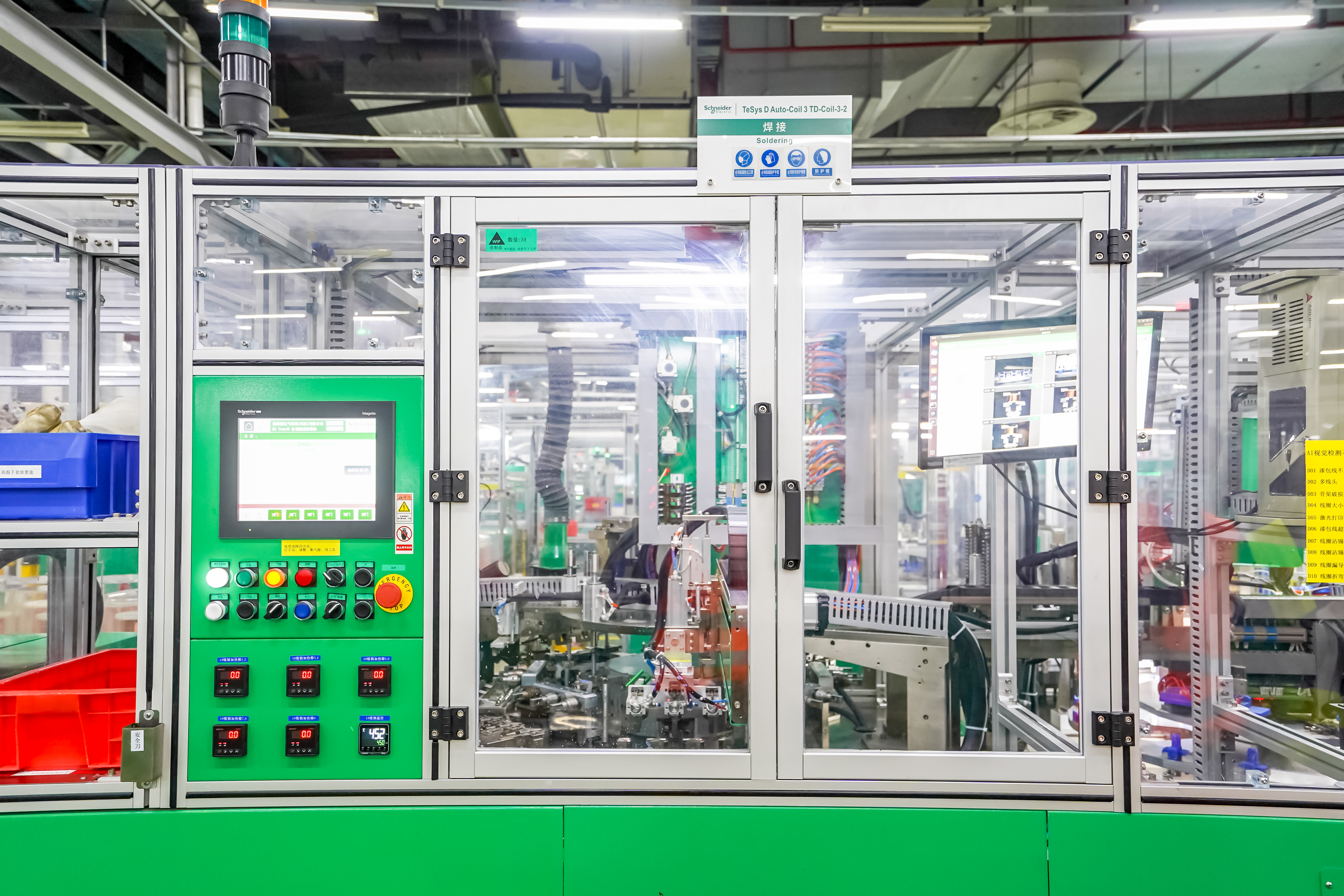
上述所提及的AI工业视觉检测平台就是第三部分数字化转型的重要组成,“在接下来的一年到两年之内,AI视觉的推广将是我们的重点之一,”李聪说道。
制造业工厂如何与云厂商合作满足数字化转型需要?
武汉工厂所生产的小型断路器、接触器等电器部件,在生产过程中会涉及大量的焊接、绕线操作,即便是用全自动化设备,也不可能使液态的焊锡、柔软的铜丝的厚度、形态完全统一。
那么就需要后续大量的产品外观质量检测。曾经使用的是人工目视检测或传统视觉检测(通过生产线上的工业照相机对每件产品进行外观拍摄,将其与标准样品对比以判断其是否有外观缺陷)。
“传统的工业制造当中,我们会通过员工每天去看,当这个产品如果一天生产15片的时候,大家看起来可能会觉得比较轻松。如果这个产品一天生产15万片,如果再去靠人看的话,那么对稳定性和准确率产生很大挑战,”李聪讲解道。
而AI工业视觉检测平台可以实现0漏检,0.5%误检率。“0漏检是件意义非凡的事情,比如用在安全相关的急停按钮开关,哪怕是0.1%的漏检率也存在巨大风险,”冒飞飞表示,“为什么我们允许0.5%的误检率呢?模型要有非常大量的样本进行训练,完全做到0其实非常难。允许0.5%,就是允许可以把好的判成不好的,然后会再检查一遍,保证检测精度。”
他认为,成功构建AI工业视觉检测平台的关键是检测模型的建模、训练和迭代。但如果采用传统的自建服务器方式这里面有两个问题,“其一是模型训练和迭代需要巨大的算力,成本非常高;其二是在进行模型训练时需要工程师到全国各地工厂去采集数据,需要投入大量的人力。”
而后施耐德电气选择与亚马逊云科技合作。
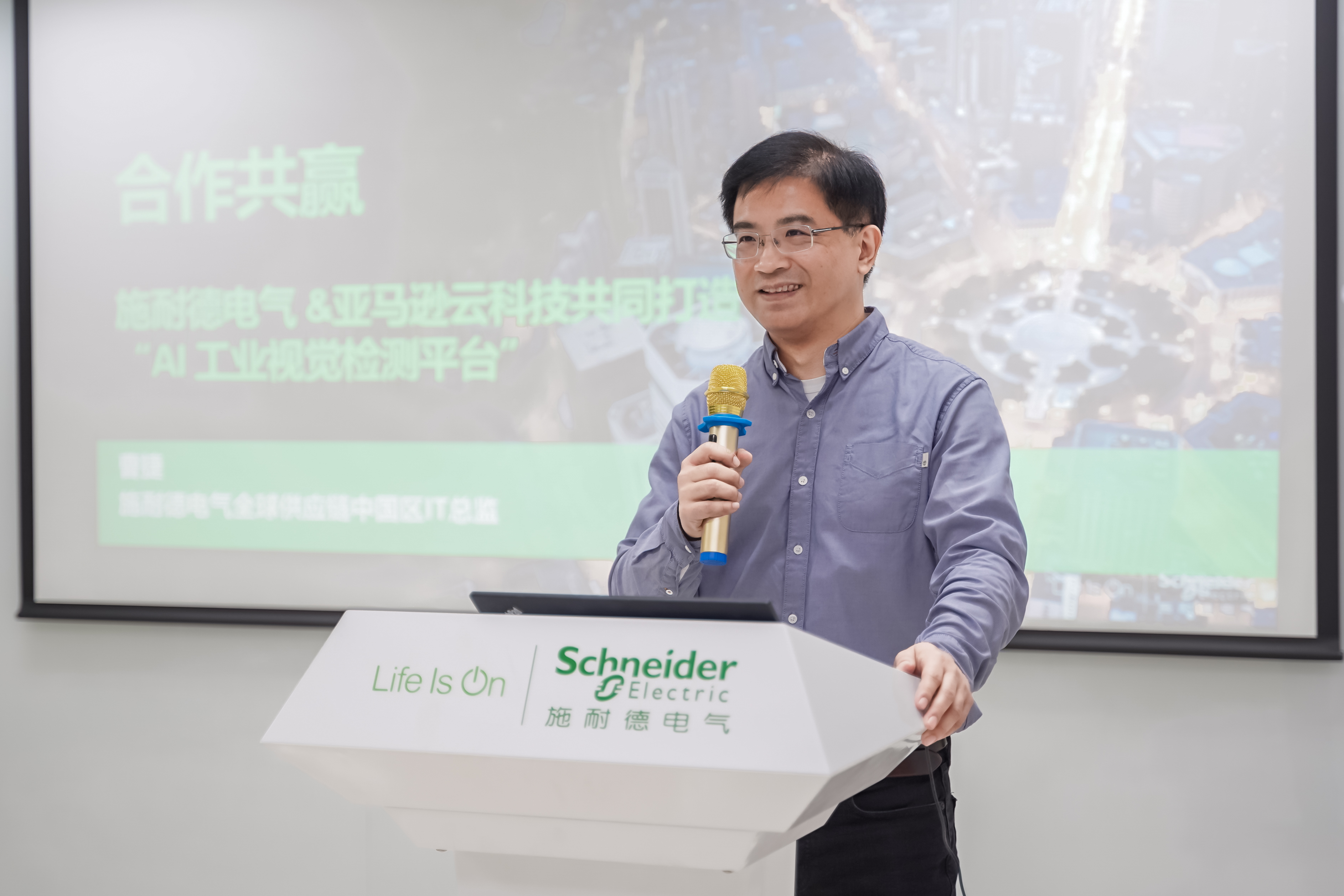
施耐德电气全球供应链中国区IT总监 曹捷
“具体来看,AI工业视觉检测平台实际上是一个云边协同的融合架构,实现云边端一体化数智闭环的系统。在云端我们可以实现海量的样本数据的存储、标注,同时在云端通过Amazon Sagemaker机器学习框架和弹性算力的提供来训练工业模型,模型训练好了以后再通过云边协同的方式,把云端的模型下发到产线边缘侧,执行边缘推理,并通过产线端的数字化和智能化的改造完成和工业控制元件的集成,从而实现一个整体的闭环回路。”施耐德电气全球供应链中国区IT总监曹捷介绍。
总结来看,就是施耐德电气收集和提供工业缺陷检测数据,采用亚马逊云科技的服务完成包括数据标注、底层机器学习的框架、算力的弹性提供,降低施耐德电气的算力成本,以及自建模型的框架选择、数据准备、环境搭建等人力成本。
Amazon SageMaker在单个工具集中提供了用于机器学习的所有组件,从而使用者能以更低成本、更轻松地在更短时间内将模型投入生产。据其介绍,可使企业开发AI模型的三年总体成本降低54%。
目前,这套AI工业视觉检测平台实现了产能大幅提升,施耐德电气已在中国区将其部署到上海、无锡、厦门等地5家工厂的9条产线中,未来还将有8家工厂、44条产线将上线。
从AI工业视觉检测这一具体的改造方案出发,可以非常清晰地观察制造业数字化转型中工业逻辑与IT技术逻辑的互动。
更深度的数字化转型目标:上下游的协同与需求指导生产
曹捷认为,IT支持的数字化项目的落地和实践,主要是通过一个两维的集成框架来推进,“横向集成指供应链价值链的集成,主要把核心业务流程数字化,同时把各个业务系统之间的数据勾连打通,从而形成数据驱动的分析、预测和智能决策的能力,提升整个供应链的效率和客户满意度。纵向集成是以单个工厂的维度、从制造管控的垂直方向,通过施耐德电气智慧工厂EcoStruxure IoT的解决方案,实现工厂的设备互联、边缘控制和在云端的应用和分析。”
李聪更进一步讲到了上下游的协同效应,“我们在部署数字化系统的时候,会把上游的供应商也整合进来,比如说它的计划、库存、订单拉动、质量管理等。同时,对于下游的客户,则是客户的所有需求、库存管理以及对客户满意度的持续跟踪。”
以应用场景为例可以更好地理解这样的上下游协同是如何在一个工厂的体系中具体体现的。
“第一个场景是全球控制运输塔台,我们在全球有7个运输控制塔台,它负责管理整个运输环节。这只是运输环节,我们正在努力打通上下游所有的信息环节,做到端到端的供应链的透明度。这意味着客户在下了订单以后,他能够知道的不仅仅是产品的运输环节,还包含整个供应链,包括上游的原材料的准备以及生产的进度,同时还有后端生产完了以后发货的整个过程进度,这是与客户端的协同。”李聪对澎湃新闻(www.thepaper.cn)表示。
他继续说道,“我们跟上游供应商端的协同有几个方面,在计划方面,供应商会知道生产的优先级和排序。在库存方面,供应商和我们一起找到最合理的、经济的库存去提高整个供应链的运营效率。我们会在系统平台上把供应商的库存纳入到我们的管理平台,一起做计划,一起做生产的排单。”
第三个质量管理的场景尤为值得注意,“在以前的质量管理思路中,更多的时候我们是被动接收一批原材料,在原材料到达工厂后,我们才能知晓这批原材料的不良比例,从而进行退货、换货等。但是现在打通和连接到供应商的整个制造过程中的一些关键参数,那么就意味着当原材料的制造过程中出现异常,就会有提前的预警。那么在一批物料有潜在质量风险的情况下,它就不会再送到工厂了。这个过程中,我们就会去分析原因、找到改进措施及替代的方案,来满足交付和供货。”
除此之外,据冒飞飞对澎湃新闻记者介绍,重点在做的还有用需求预测指导生产,“从需求端我们可能会用一些AI的方法感知市场上的一些需求,同时结合施耐德电气本身的一些精益指标去做预测,指导生产。”
吴军在《智能时代》一书中曾论述道,“生产越来越过剩,需求拉动经济增长的模式变得不可逆转。”





- 报料热线: 021-962866
- 报料邮箱: news@thepaper.cn
互联网新闻信息服务许可证:31120170006
增值电信业务经营许可证:沪B2-2017116
© 2014-2025 上海东方报业有限公司