- +1
超精密磨削与仿真技术
近日,山东大学姚鹏教授团队以“柱面微透镜阵列的精密磨削”为题发表文章于《光学 精密工程》2021年29卷第7期,并被选为封面文章。
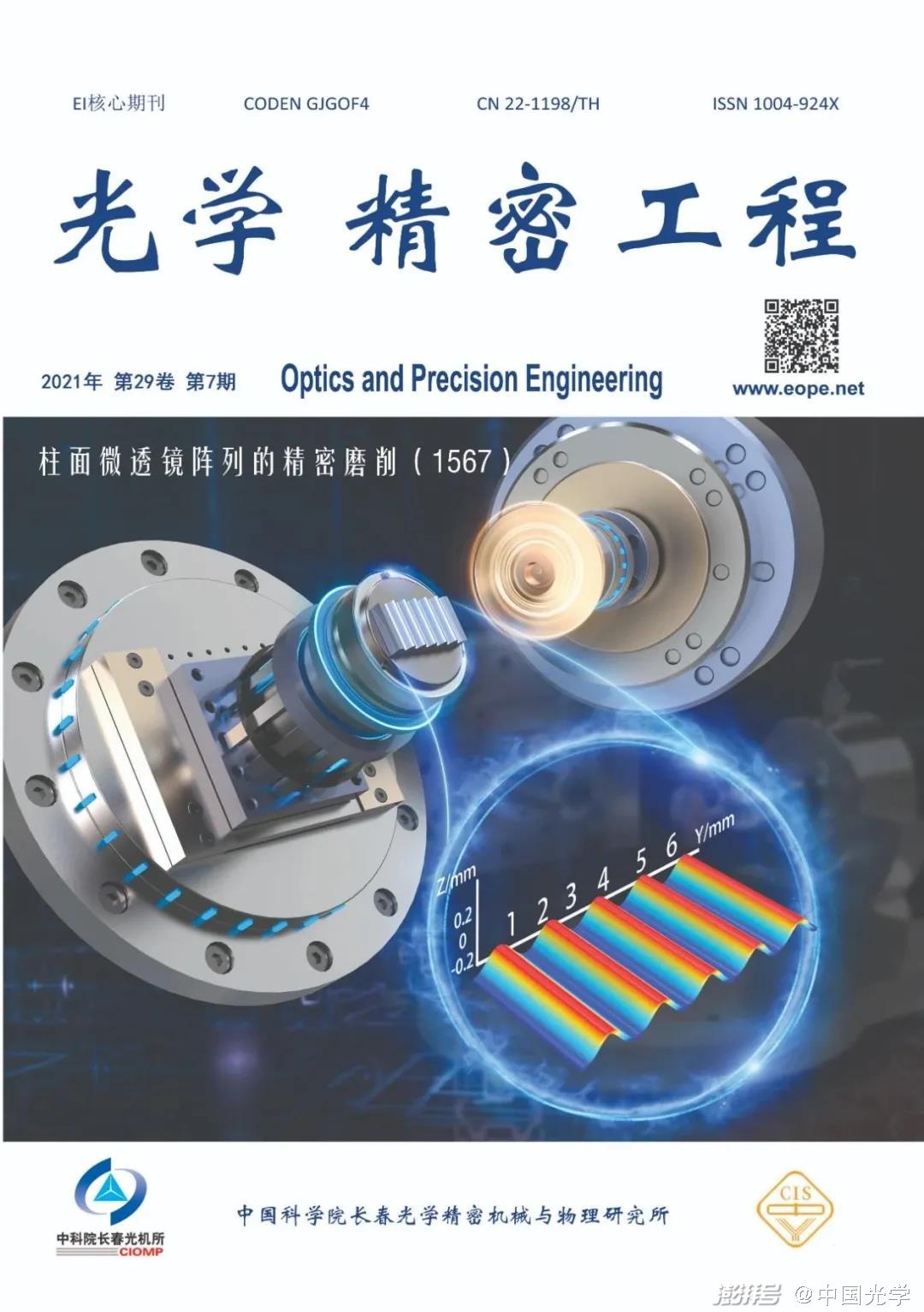
《光学 精密工程》 2021年 29卷 第7期 期刊封面
柱面微透镜阵列元件是由柱面结构深度为微米级的透镜组成的阵列,不仅具有传统透镜的聚焦、成像等基本光学功能,而且具有单元尺寸小,集成度高的特点。在军用,民用,天文等领域有着广泛应用,例如激光制导,激光光束均匀化以及三维成像等等。
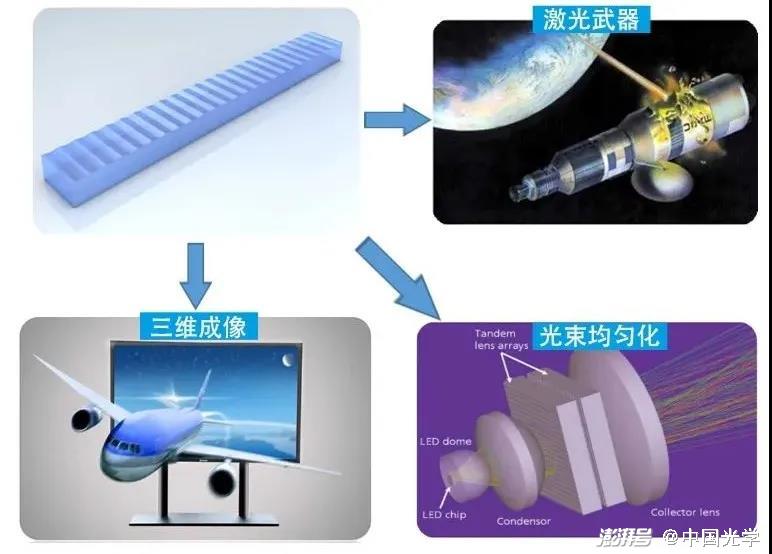
图1 柱面微透镜阵列元件的应用
鉴于制造成本和制造难度,国内外厂家提供的柱面微透镜通常是普通圆柱截面,但非圆截面柱面微透镜可以进一步简化光学系统,降低系统重量,对航空航天应用具有更加重要的意义。非圆截面柱面微透镜国外可以定制,但成本高,供货期长,有些甚至是受限的卡脖子光学元件,国内尚无法提供满足要求的此类光学元件。采用模压技术可以大大降低成本,RB-SiC作为模具材料用于玻璃模压,相比传统镀镍模具形状保持性好,寿命长,是玻璃模压模具的理想材料,但加工难度大,目前磨削加工可以说是唯一的选择。
传统的磨削方法采用微小磨具进行超精密磨削加工,加工效率低,砂轮磨损严重,需要进行多次繁琐的砂轮修整,不仅降低加工效率,而且增加编程和对刀过程,加工难度大。因此,开发高效率的磨削加工方法具有很高的研究价值。
与传统的加工方法相比,本文采用成形砂轮进行复映磨削加工,能够极大地提高加工效率。采用成型磨削加工,需要在砂轮上修整出和柱面微透镜阵列对应的高精度微细轮廓结构,目前砂轮修整技术主要有机械修整,激光修整和电火花修整。将成型砂轮装夹在平面磨床主轴上,选定合适的磨削参数,可以实现一次往复磨削加工成型,无需进行多次修整,效率极高。同时,成型磨削加工降低了对机床设备的要求和编程的难度,无需多轴联动机床和复杂加工程序,对机床操作人员素质要求不高,具有很强的现实意义。
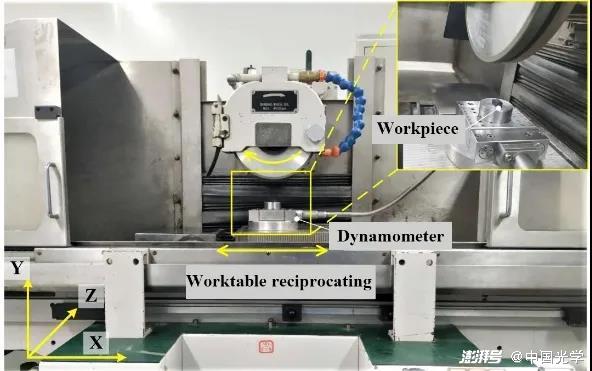
图2 实验装置
为了能准确的把握成型磨削加工后工件的表面质量,本文使用MATLAB对实验砂轮和磨削过程进行了仿真。通过分析实验砂轮和磨粒的特征,建立砂轮的数值化模型,研究砂轮表面磨粒与工件的几何相互作用机理,形成对工件表面材料的划擦和去除,建立磨削表面的仿真模型。对比了磨削实验和仿真的工件面形误差的PV值、粗糙度Ra和Rz值的对比,仿真模型的偏差分别为5.78%,17.3%和12.9%,证明了本文提出的仿真模型的有效性。
磨削仿真模型的意义在于可以在开展磨削实验之前对磨削加工精度和表面质量结果进行预测,根据实验所选择的砂轮的特征,以及磨削工艺参数等实验条件,模拟分析此实验条件下的得到的工件质量是否符合技术要求。在不满足技术要求的情况下,可以改变实验条件,优化实验参数指导磨削加工。
这种以超精密加工对象的精度和表面质量为目标,选择和优化砂轮与磨削参数的仿真方法,节约大量磨削加工工艺试验的时间和成本,对提高磨削加工效率,推动超精密磨削加工技术更广泛的应用具有重要的意义。
论文信息
叶震, 姚鹏, 于世孟, 等. 柱面微透镜阵列的精密磨削[J]. 光学精密工程, 2021, 29(7):1567-1579.
论文地址
DOI:10.37188/OPE.2020.0612
团队介绍:
1. 作者
(1)第一作者
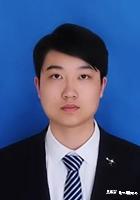
叶震,助理研究员。2020年于山东大学获得学士学位。主要研究方向为磨削与精密加工技术。
(2)通讯作者
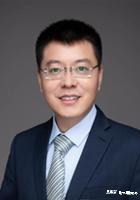
姚鹏,教授,博士生导师, 2011年于日本东北大学获得博士学位,主要研究方向为超精密加工技术、多能场复合精密加工技术、超快激光微纳加工技术。国际磨粒技术委员会(ICAT)青年委员,机械工程学会生产工程分会全国磨粒技术委员会和精密工程及纳米技术专业委员会委员。在国内外高水平学术期刊及会议发表论文60余篇,获教育部技术发明一等奖,机械工业协会二等奖,上银优秀机械博士论文奖指导教师,多个精密加工领域学术会议的优秀论文奖,第一发明人授权发明专利17项,PCT 2项,研究成果应用于航空航天企业和科研院所。
(3)团队负责人
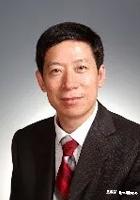
黄传真,教授,博士生导师,国家杰出青年科学基金获得者(2006),“万人计划”国家高层次人才特殊支持计划领军人才(2017),1994年于山东工业大学(现山东大学)获得工学博士学位,主要研究方向为高效精密加工、磨料水射流与特种激光加工、陶瓷刀具与结构陶瓷材料、微纳制造、生物增材制造。
2. 团队研究成果
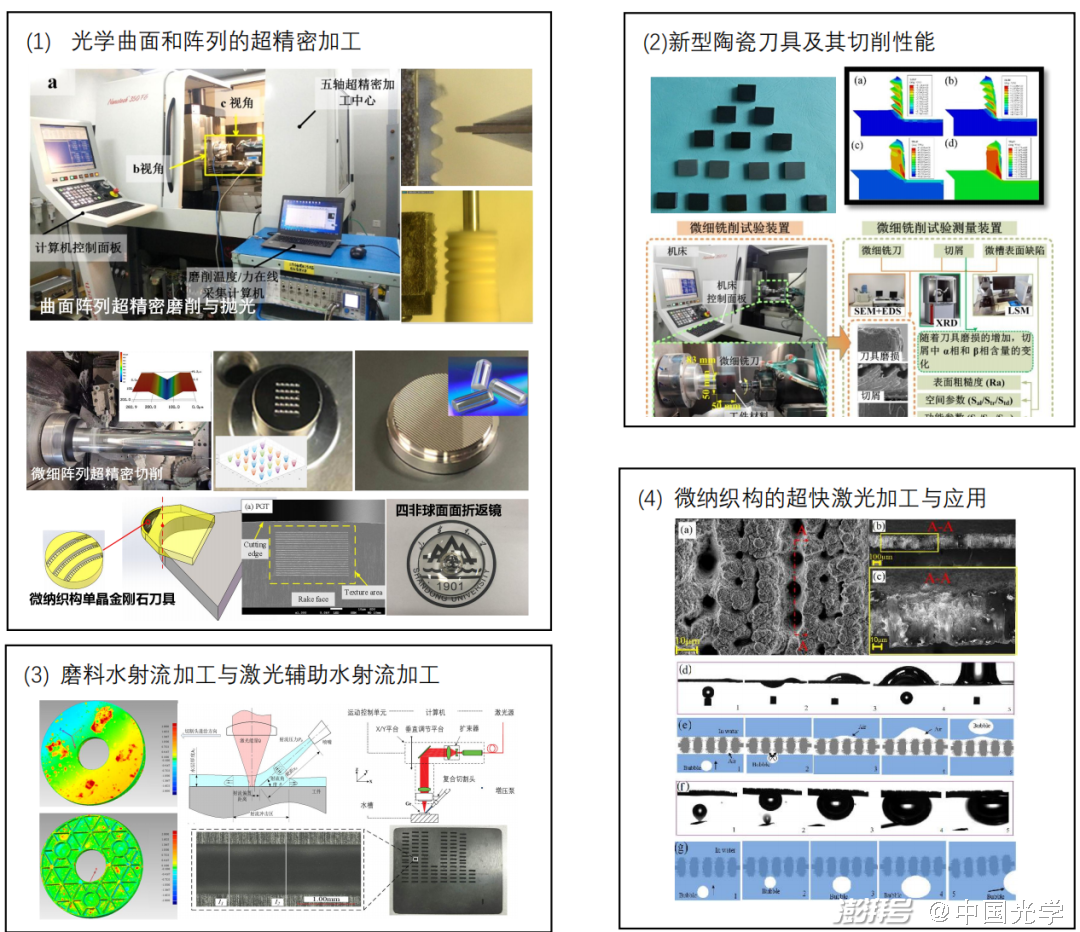
监制 | 赵阳、袁境泽
编辑 | 赵唯
欢迎课题组投稿——新闻稿
文章转载/商务合作/课题组投稿,微信:447882024
带您每天读1篇文献!加入>Light读书会
本文为澎湃号作者或机构在澎湃新闻上传并发布,仅代表该作者或机构观点,不代表澎湃新闻的观点或立场,澎湃新闻仅提供信息发布平台。申请澎湃号请用电脑访问http://renzheng.thepaper.cn。





- 报料热线: 021-962866
- 报料邮箱: news@thepaper.cn
互联网新闻信息服务许可证:31120170006
增值电信业务经营许可证:沪B2-2017116
© 2014-2024 上海东方报业有限公司