- +1
匠心丨“国宝级”电焊工陈庆城:每年为20余艘船合拢焊接
钻研焊接20多年,陈庆城成为一名“国宝级”电焊工。他说,通过电焊技能改变命运。
作为广船国际总装部撘载课高效焊接工段工长,陈庆城带领50多位技能突出的电焊工,负责船舶合拢时的焊接工作。这项工作难度高,且不能有差错,陈庆城的压力不小,若工人碰到搞不定的焊接难题,他得亲自出马解决。
“最小的船有5万吨,大的有30多万吨。一艘船合拢时的焊接工作,要做2-3个月。”12月5日下午,陈庆城告诉澎湃新闻(www.thepaper.cn),他的团队一年大概要为20多艘船的合拢做焊接。
在公司,不少人喊陈庆城为“陈大师”。如何炼成“电焊大师”的?陈庆城的回答很简单:在实践中不断总结经验,通过解决问题提升技术。
澎湃新闻了解到,陈庆城把困扰船舶建造生产难题转化为技术攻关的课题,其多项成果在国内《焊接技术》《电焊机》《广东造船》等核心期刊发表论文,目前已有78项技改创新成果在生产实践中得到推广应用。
“焊接容易学,而且相关技能比赛很多,容易熬出头。只要熟练掌握了技术,不愁工作。”陈庆城表示,焊接的未来应该走向机械化、自动化,他已在尽力推广焊接的机械化,以此减轻电焊工的劳动强度。
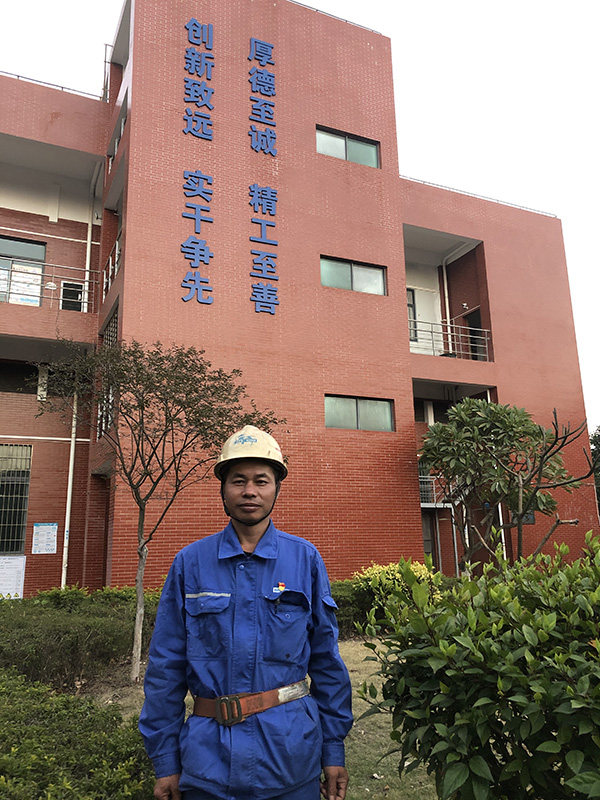
陈庆城 澎湃新闻记者 陈绪厚 图
曾参与众多重大工程建设
今年44岁的陈庆城是广东梅州人,出生于农村家庭,于1993年进入广州造船厂技工学校学习船舶焊接。三年后,陈庆城进入中船集团旗下的广船国际工作。
“在学校时,既学习理论知识,也有实操机会。”陈庆城表示,最初,他主要学习手工电弧焊,这种焊接手法最为常见、实用,看上去很简单,很多没有经过专业训练的人也能做,但 “易学难精”,要真正达到行业标准,需要很多年的技术沉淀。
进入广船国际后,因焊接功底较好,陈庆城进入压力容器部,“加入该部门的都是技术能手”,他们所面临的挑战也是巨大的。压力容器部关乎整个船舶的加压系统,若焊接有问题,可能会发生爆炸等安全事故,因此对焊接的要求非常高,“每个焊缝都要做X光拍片,看焊缝里面有无缺陷,要做到100%合格”。
“不能出一点问题。”陈庆城表示,每个人烧的焊缝,都会打上带着自己编号的钢印,要对这个焊缝永远负责。在当时20多人的团队里,陈庆城是年轻人,他跟着老师傅学技术,积累经验,从比较简单的B类焊接做起,约一年后开始做A类焊接。
在压力容器部工作六七年后,陈庆城的焊接技术逐步成熟。他说,从一开始就接受这种高质量要求的锻炼,对他的技术提升有非常大的帮助。
上世纪90年代末,陈庆城所在的压力容器部开始业务转型,承接外面的钢结构焊接项目。陈庆城介绍说,他们曾参与虎门大桥、北京植物园温室、香港迪士尼乐园等一些列项目的钢结构焊接工作。
让陈庆城印象最深的,是虎门大桥的焊接工作。虎门大桥是珠江口大跨径悬索桥,线路全长15.76千米,主桥全长4.6千米,于1997年6月建成通车,是我国第一座真正意义上的大规模化悬索桥,曾获詹天佑土木工程奖。陈庆城表示,对于电焊工来说,大桥合拢时焊接最难,“平时可以平焊为主,但合拢时不具备这样的条件,会有很多的仰焊”。
根据焊接位置不同,焊接可分为平焊、立焊、横焊、仰焊等。一般而言,仰焊最难,电焊工的视角朝上,不利于操作,而且铁水会往下坠,容易达不到标准。陈庆城记得,在虎门大桥合拢时,涉及到很多斜仰焊,需要搭架子,但架子很小,不但操作难度高,还不好避让掉落的火花,常被烫伤。
“整个部门都出动了,仅大桥合拢时的焊接,就做了半年。”陈庆城告诉澎湃新闻,虎门大桥的桥面是箱体,里面有很多结构,当时他多在狭窄的箱体内作业,且是夏天,里面的温度非常高,不一会就汗流浃背了。
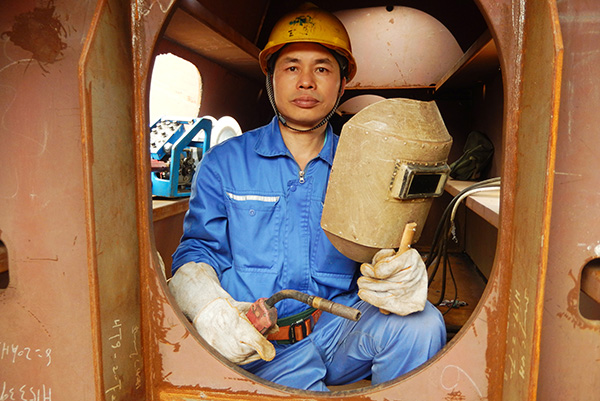
陈庆城在船舶内从事焊接作业 受访者供图
一年要为20多艘船舶合拢焊接
2000年前后,由于部门合并、业务调整,陈庆城所在的部门不再做钢结构的焊接,而是为造船服务,专门负责船体合拢时的焊接工作。这对焊接的要求也很高,焊缝需要用X光拍片和超声波来检测是否合格。
“船舶环境复杂,结构多,空间小。有些位置被阻挡,操作难。”陈庆城和团队遇到的最大难题是,会有垂直地面15米长的缝需要焊接,若采用常规的二氧化碳气体保护焊,劳动强度大,效率低,焊接质量受操作技能影响大。
经过研究,并从国外造船业借鉴经验,陈庆城和团队引进了垂直气垫焊,通过操作机器完成焊接,“一处15米长的焊缝,2-3个小时就可以完成,若还用原来的焊接方法,得花2-3天”。
解决了立焊难题后,又遇到横焊对接缝质量不稳定的问题,“焊道比较多,主要依赖手工操作,不仅劳动强度大,也常常不符合质量标准”。陈庆城直言,这个问题多年来一直是瓶颈,没有好的解决办法。
2018年,陈庆城和团队通过研究改进了设备,总结出埋弧横焊的方法,取得了很好的效果,“烟尘小了,没有了弧光,质量也稳定,同行都想来学”。今年,陈庆城和团队再次改进设备,把设备改得更为轻便,仅两个人就能搬动。
近20年来,陈庆城和团队一直负责为船舶合拢的焊接,他们所负责的船舶从数千吨也逐步升级到30多万吨。“一艘船的合拢焊接要2-3个月。”陈庆城说,50多人的团队一年要为20多艘船舶完成合拢焊接。
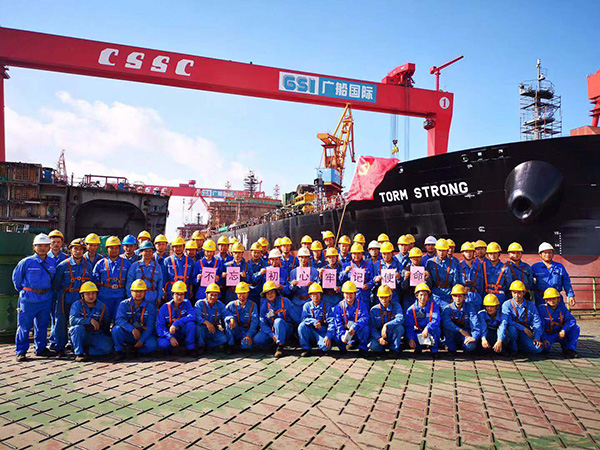
陈庆城的团队有50多人,专门负责船舶合拢时的焊接任务。 受访者供图
解决造船焊接技术难题百余项
在焊接领域扎根24年,陈庆城共解决造船焊接技术难题100余项,技改创新成果78项,获国家专利授权授理22项。他为能端稳焊枪练肿了胳膊,不惧电弧光灼伤眼睛和烫伤手臂,摸索、练就出船舶狭窄空间环境的“镜子反射法焊接”和“听声辨成型法”的独门绝技。
在国家品牌国家利器“和平方舟”号医院船建造中,该船硬件设施相当于三级甲等医院的水平,然而船体结构复杂狭小,技术要求极高,很多焊缝位置躺着焊接都无法看到。陈庆城迎难而上,研究出“听、快、准、狠”操作特殊焊接绝技并推广,其焊缝X光拍片探伤一次合格率达100%,由船代表不定点随机抽查的25张X光片全部评定为I级片。
在媲美豪华邮轮“皇冠上的明珠”的Gotland豪华客滚船建造中,为克服重心控制薄板建造工艺这一业内公认的难题,陈庆城从薄板刚性、焊接应力、结构失稳找原因攻关,研究出薄板立对接单面焊双面成形变速焊焊接技术、薄板FAB,为船舶薄板高效建造提供新的焊接技术,同时将薄板轻便型埋弧焊、全位置摇摆小车等高效焊接技术进行广泛应用,打破豪华客滚船搭载薄板高效自动焊的盲点,解决了薄板变形“橘子皮”难题,节约了人工和材料成本100余万元。最终该船上建薄板焊接施工周期缩短了26天,创造经济效益300余万元。
在世界首艘全电力静音推进科学考察船“嘉庚”号建造过程中,针对该船多波束装置的160个换能器和探头焊接精度误差控制在±1.5mm的高要求,同时要克服焊接空间狭窄和焊接量大等困难,陈庆城临危受命,从改进工装和焊接方法着手,经过无数次的尝试发明了“加长和可变化式焊枪”,同时研究出一套二氧化碳气体保护焊操作方法和不规则退焊分散法两项新焊接工艺技术,最终按期完成了生产任务。
陈庆城表示,在实践中,肯定会遇到很多问题,要去研究总结,去解决问题。他喜欢琢磨焊接,“从外观上看,焊接成形要漂亮,其关系到设备、材料、参数、操作手法等因素,但内部更为重要,要重点琢磨,不断优化操作方法,总结经验”。
凭借多年的技术积淀,陈庆城把困扰船舶建造生产难题转化为技术攻关的课题,其多项成果在国内《焊接技术》《电焊机》《广东造船》等著名核心期刊上发表论文,系统介绍了各种典型项目的技术规范和操作要领,且目前已有78项技改创新成果在生产实践中得到推广应用,平均每年为公司创造经济效益超过1000万元。
陈庆城还利用国家级技能大师工作室平台,重新修订了《焊接工艺与规范手册》、汇编《薄板分段施工工艺手册》、编写《CO2气体保护焊各种位置焊缝成形焊工操作规范手册》、制作《船舶电焊工微课》,成为船舶电焊工学习及指导的重要资料;他主编出版了《船舶电焊工/焊工》(初中级工、高级、技师及高级技师)等各个级别一套船舶主体工种岗位培训教材,填补了企业技能等级认定教程空白。
技能大赛是选拨人才的好途径
随着焊接技术越来越精湛,陈庆城获得的荣誉也越来越多,他是全国劳动模范、全国技术能手、全国五一劳动奖章、中国青年五四奖章的获得者,曾获得中央企业“百名杰出工匠”等荣誉称号,入选国防科工委“511人才工程”,是《技能中国》宣教片18位技能大师之一、国家级技能大师工作室带头人,享受国务院政府特殊津贴。他被同事们称为“陈大师”,被媒体形容为“国宝级”的电焊工。
年轻时,陈庆城的人生目标是在广州安家,有一份稳定、体面的工作。如今,这些早已实现,他说是技能改变了自己的命运。
作为团队中的“老师傅”,陈庆城发现,如今很难招到电焊工,“年轻人不愿意干”,其工作环境的“脏”“累”“苦”,让很多人望而却步。
在陈庆城看来,焊接的未来肯定是走向机械化、自动化,主要由机器来作业,工人操作机器即可。因此,他也在有意识地推广焊接的机械化,这可以提高生产效率,减轻电焊工的劳动强度,改善其工作环境。
“我有一个徒弟,才25岁,已经多次拿过省市技能大赛的第一名。”陈庆城重视电焊人才培养,先后为企业培养出了高级工127名、技师27名、高级技师4名、1名全国技术能手。他的多名徒弟也已经成为船舶焊接领域的技能大师,徒弟张八虎、黄溶在参加 44 届世界技能大赛广东选拔赛中获得了第一名和第三名,并获“广东省技术能手”,并带培焊工冯文虎、雷振锋参加粤港澳大湾区焊接技能大赛分别获得金奖、银奖。
陈庆城说,对于招来的年轻人,他们会在部门、公司内进行技能比拼,再去参加省市的技能大赛,“技能大赛是选拨人才的很好途径”。他认为,“行行出状元”,电焊从业者要发扬精益求精的工匠精神,不断钻研创新,提升自己的技术。





- 报料热线: 021-962866
- 报料邮箱: news@thepaper.cn
互联网新闻信息服务许可证:31120170006
增值电信业务经营许可证:沪B2-2017116
© 2014-2024 上海东方报业有限公司